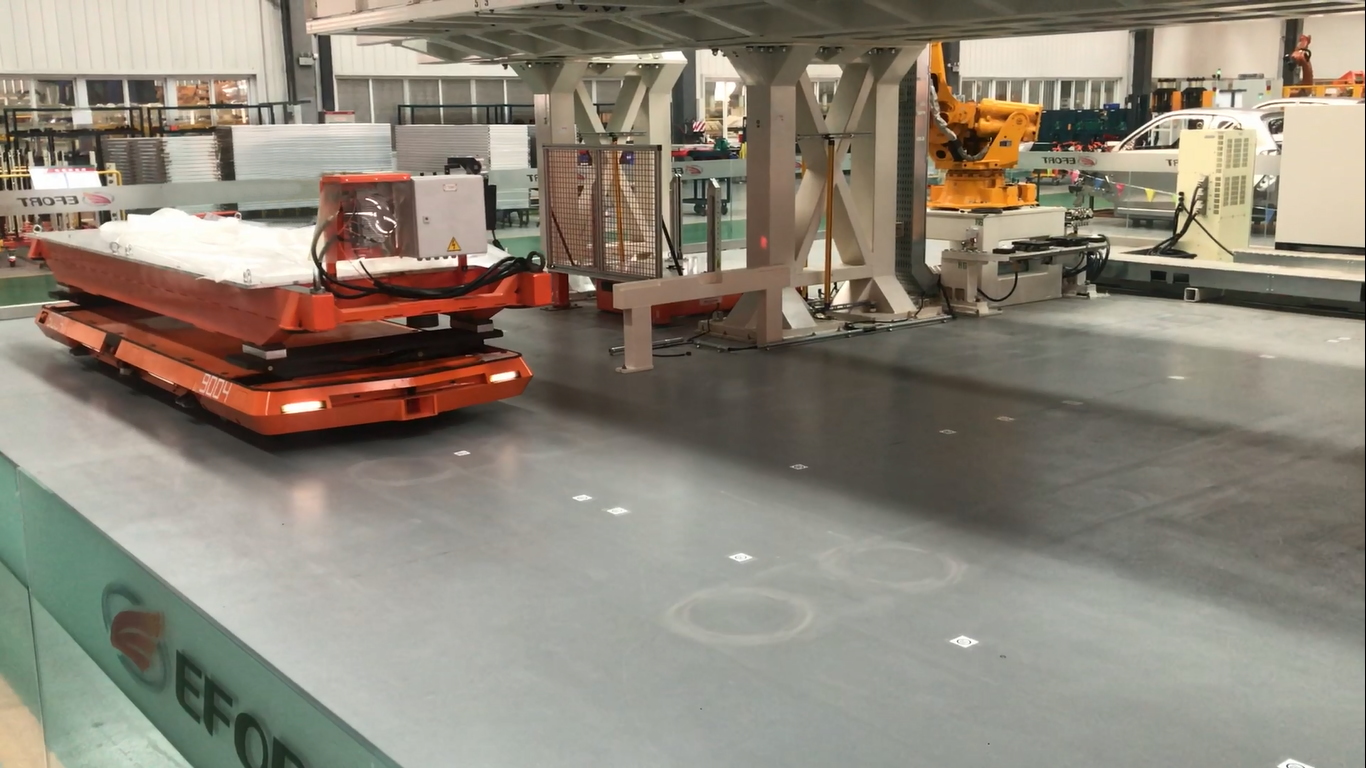
Applicazioni
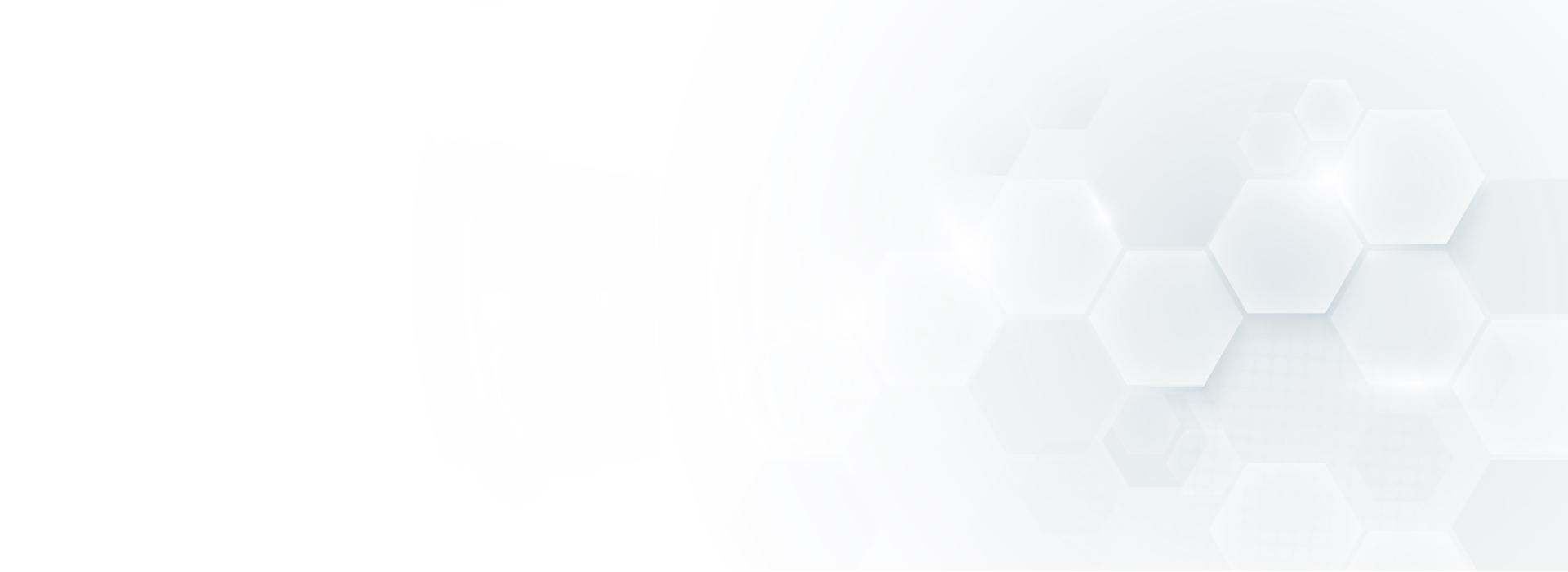
Linee Multiuso
Attualmente, la maggior parte delle catene di montaggio esige linee flessibili, capaci di produrre vari modelli in un mix casuale, con l’ingresso di modelli futuri. Questo tipo di approccio esige l’istallazione di attrezzature complesse (tavoli giratori, mulini, scivoli, ecc.) a partire dal primo modello, con grande investimento fin dall’inizio. Allo stesso tempo, questi sistemi sono abbastanza inefficienti, facendo si che l’efficienza della linea cada (dovuto al IMTBF basso e MTTR molto alti). L’area occupata deve considerare lo spazio necessario per la logistica lungo la linea (bancali, operazioni manuali di carico/scarico, ecc.), dove tutti i pezzi di tutti i modelli devono essere disponibili allo stesso tempo.
Dovuto alle ragioni sopra elencate, la maggior parte delle catene di montaggio generalmente riesce a raggiungere appena 4 modelli, dovuto alle aree disponibili delle fabbriche. Oltre a questo, la tassa di saturazione dei lavoratori è solitamente abbastanza bassa considerando che loro devono aspettare che i robot e attrezzature completino le loro sequenze prima di iniziare la procedura di carico/scarico.
L’idea della linea multiuso è nata per risolvere tutti questi problemi, riducendo l’investimento per il primo modello e dell’area occupata, migliorando l’efficienza della linea e la saturazione dei lavoratori.
Caratteristiche principali
- Produzione in lotti, usando AGVS per sostituire accessori/bancali per cambio di modello (senza fermare la produzione)
- Investimento più basso per il primo modello (la linea è sviluppata con una struttura con molta pendenza, con una integrazione della AGV partendo dal secondo modello)
- Maggior efficienza, evitando tavoli giratori, mulini, scivoli o altri sistemi complessi installati lungo la linea per sostituzione di modello
- Aperto alla produzione di vari modelli, senza restrizioni per future integrazione di modelli
- Ottimizzazione delle aree, dividendo le linee di saldatura e logistica (preparazione di bancali/stock di attrezzatura) in aree specifiche
- Maggior saturazione della mano d’opera. I lavoratori preparano tutti i bancali in un’area di logistica dedicata (Supermarket kitting area), senza vincolare i tempi di ciclo della linea di saldatura (senza perdita di tempo)
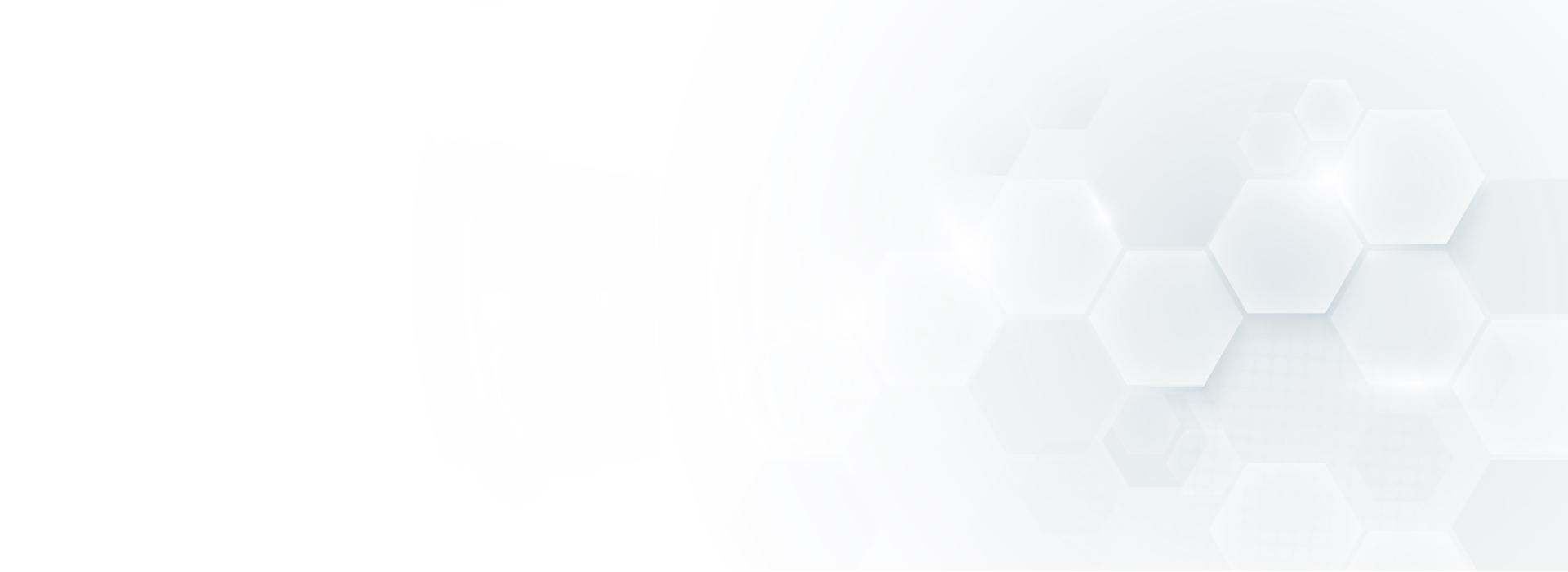
Saldature MIG/MAG
Le saldature ad arco sono una forma ancora molto diffusa di saldatura. Come il suo nome suggerisce, la saldatura ad arco usa un arco elettrico per sciogliere i materiali prima di unirli. Una fonte di alimentazione è usata per creare un arco elettrico tra un elettrodo e il foglio di metallo da unire. Questo arco elettrico può arrivare a temperature superiori a 3500°C, che è forte sufficiente per sciogliere metalli come l’ acciaio carbonio. L’area di saldatura è solitamente protetta da gas di protezione, vapore o escoria. Questo succede perché l’aria atmosferica può interagire con la pozza di fusione causando ossidazione.
Sia il MIG (Metal Inert Gas) che il MAG (Metal Active Gas) utilizzano un elettrodo di filo solido continuo (filo di saldatura), che è riscaldato e alimentato nella piscina della saldatura partendo da una bocchetta del saldatore. I due materiali vengono quindi fusi insieme formando una giuntura.
L’unica differenza tra il MIG e un MAG è il tipo di gas di protezione utilizzato (fornito per mezzo della bocchetta della saldatrice). La composizione del gas di protezione è importante, perché ha un effetto significativo per la stabilizzazione dell’arco nel trasferire il metallo sul profilo della saldatura, nella penetrazione e nel grado di schizzi. La saldatura MIG usa gas inerti o misture di gas come gas di protezione. Argon e Elio o misture di Ar/He sono gas inerti e normalmente usati per la saldatura MIG di materiali non ferrosi come l’alluminio. I gas inerti non reagiscono con i materiali di riempimento o la pozza di fusione. La saldatura MAG usa invece gas di protezione attivi. Questi gas possono reagire al contatto con i metalli aggiunti attraverso l’arco e dalla pozza di fusione, affettando la chimica e proprietà meccaniche risultanti.
La saldatura MIG e MAG è il processo di saldatura ad arco più comune nelle principali industrie, come quella automotiva, ferroviaria, GI, tra gli altri. Tra i loro principali vantaggi possiamo citare:
- Adatta per saldature ad alta velocità con una qualità di saldatura molto alta (permettendo un grande volume di produzione)
- Maggior qualità (confronto ad altri sistemi di saldatura ad arco)
- Processi versatili che permettono di saldare vari tipi di metalli e leghe
- Attrezzatura di saldatura semplice (confronto ad altri processi di unione)
Competenza e supporto GME
Carrozzeria, veicoli fuoristrada, camion, treni, industria degli elettrodomestici, tra gli altri. Tutti utilizzano processi di saldatura basati principalmente sulla saldatura a punti e sulla saldatura MIG/MAG. Entrambi richiedono una forte specializzazione e capacità tecnica.
La GME ha sempre coperto un ruolo fondamentale, appoggiando i principali players del mercato nello sviluppo di soluzioni turnkey. In particolare la saldatura MIG/MAG esige un’attenzione particolare sui seguenti punti:
- Piano di fissaggio – Alte temperature raggiunte intorno alla matassa di saldatura possono causare una distorsione strutturale nel montaggio finale. Per questo è importante sviluppare un piano di fissaggio adeguato, evitando la deformazione dei pezzi durante il processo di saldatura
- Schizzi di saldatura – Durante il processo di saldatura ad arco, è abbastanza comune vedere alcun schizzo di saldatura. Per garantire una buona qualità di saldatura (anche dal punto estetico) e evitare qualsiasi problema nei seguenti processi (per esempio, il processo di saldatura di lettini frontali generalmente richiede l’aggiunta di dadini come processo di accoppiamento ad alta precisione) l’area intorno alla saldatura e i punti di saldatura devono essere coperti per evitare che gli schizzi entrino in contatto diretto con i pezzi
- Protezione – Proteggere tutti i cavi di alta temperatura e gli schizzi di saldatura, usando un coperchio a prova di fuoco
- Localizzatori di cucitura/telecomandato di cucitura per saldatura ad arco automatico – I robot generalmente sono usati per migliorare la qualità e la produttività ma è necessario garantire la reperibilità e la precisione di tutti i pezzi che devono essere saldati, per garantire lo stesso risultato in ogni ciclo. Questo non sempre è possibile in certe industrie (esige costi molto alti) quindi il processo di saldatura deve essere adattato a differenti forme e posizioni dei pezzi (dentro una determinata fascia). Riguardo la saldatura ad arco, i robot possono essere accessoriati con sensori speciali per verificare la posizione della cucitura e correggere il suo cammino durante il processo di saldatura, detectando lo spostamento tra la posizione nominale e reale ad ogni ciclo
- Ambiente salutare – Un ambiente salutare deve essere garantito, usando sistemi di aspirazione di aria localizzati in ogni operazione di saldatura e isolando tutte le aree di saldatura dagli occhi dei lavoratori (con barriere fisse o tende rosse)
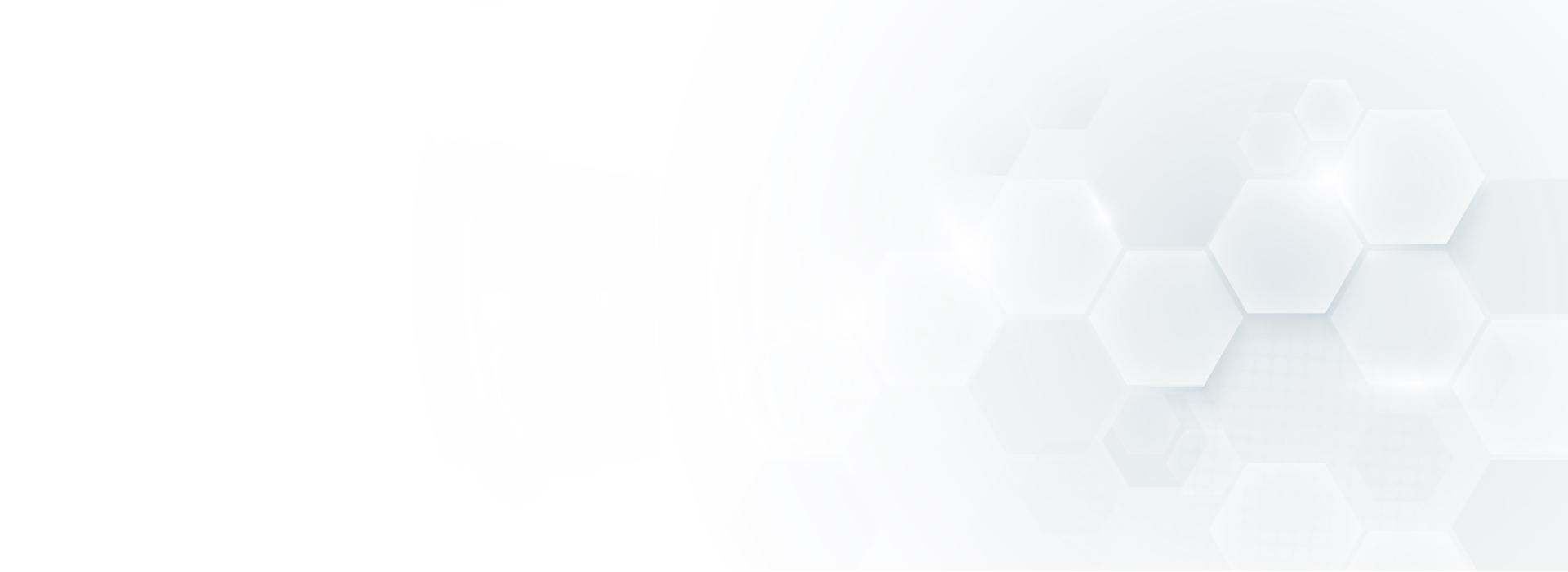
Co-Design & Ingenieria Simultanea
Oltre ai normali processi turnkey, che la GME normalmente realizza per i suoi clienti, certe volte nasce la necessità di sviluppare un processo che possa essere adattato efficientemente alle caratteristiche del prodotto, mettendo in conto le condizioni delle linee di produzione nella pianta del cliente.
Quest’attività, comunemente chiamata di “co-design”, consiste nella ricerca e sviluppo di soluzioni di processo insieme ai clienti, ingegneria e cantieri, analizzando le caratteristiche di un nuovo prodotto insieme alle disponibilità reali della pianta del cliente, o sia, una pre-valutazione rispetto alla misura che può essere applicata per un progetto nuovo o retooling.
Le specificazioni iniziali per creare un co-design basicamente rispondono alle seguenti sequenze:
- Monitoramento del processo
- Analisi del flusso logistico
- Creazione di layout 2D/3D per definire lo spazio
- Analisi del ciclo di produzione
- Simulazione di accesso dei robot/attrezzatura
- Analisi Ergonomica e delle tempistiche
- Definizione delle specificazioni dell’attrezzatura
- Quantificazione e monitoramento dei costi
- Analisi FEM
- Creazione del quaderno degli incarichi con tutte le specificazioni per rendersi disponibili nel Mercato
Oltre a ridurre i costi e le tempistiche, l’ingegneria simultanea diminuisce le chances di, durante uno stadio più avanzato, dover modificare il prodotto per causa di problemi imprevisti. In relazione ai gruppi di progettazione, il maggior involgimento tra le varie aree migliora il compromesso del progetto.
La GME generalmente lavora insieme al dipartimento di prodotto del cliente, in questo modo riesce a sviluppare soluzioni visionando il miglior costo. I pezzi di macchina, piano di metodo, processo, generalmente sono valutati per ottimizzare al massimo, controllando il loro storico di processo di ogni caso.
Studio dei Casi
Caso 1
- Riduzione dell’investimento fino al 30%
- Nuovo modello sviluppato insieme alla ingegneria di manifattura
- Specializzazioni tecniche del cliente sviluppato insieme all’equipe GME
Caso 2
- Riduzione dell’investimento fino al 40%
- Dispositivi compatibili con GEO
- Dispositivi compatibili con RESPOT per vari modelli
- Artigli compatibili per vari modelli
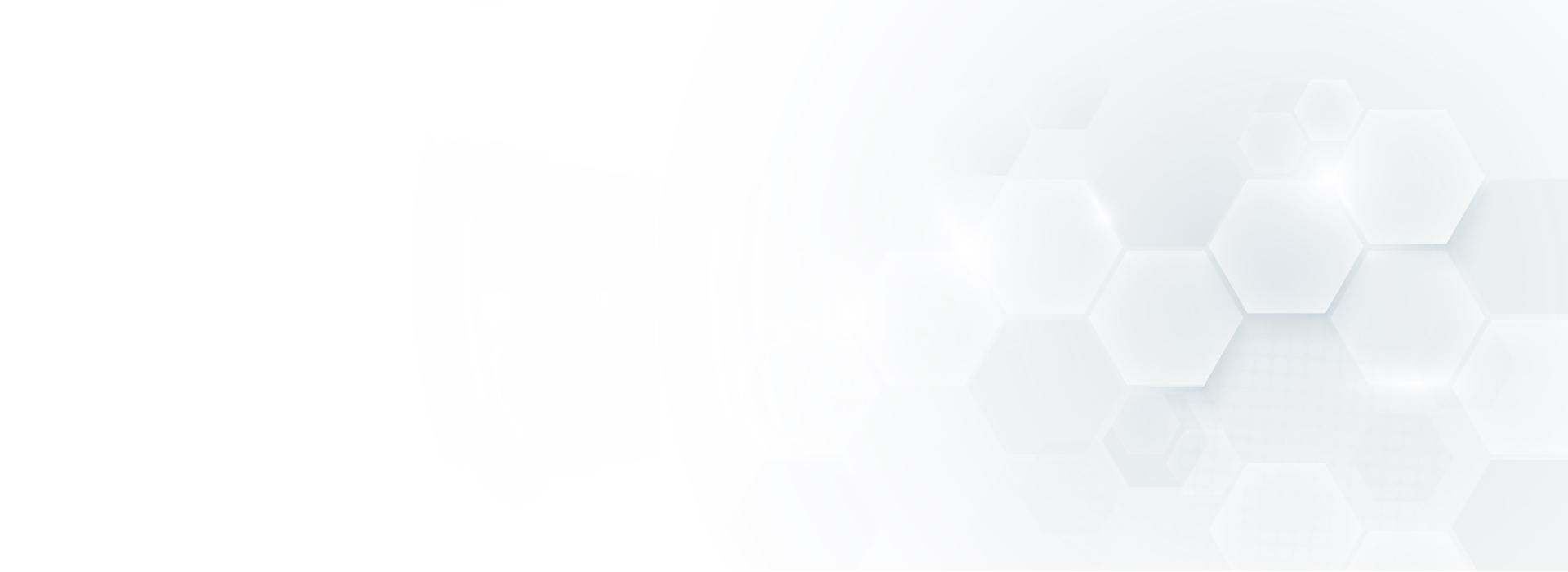
Free Expression
Il nome “Free Expression” si deve ad una sfida definita dai nostri principali clienti, dove tutti i concorrenti sono liberi di sviluppare una nuova proposta per la linea di porte Davanti e dietro, senza nessuna restrizione in termini di layout.
La proposta della GME è stata selezionata come la migliore, introducendo un nuovo concetto dove entrambi i lati destro e sinistro sono prodotti sulla stessa linea.
Economia ottenuta in confronto alle soluzioni tradizionali:
- Robot: -30%
- Macchine integrate: -50%
- Sistemi di chiusura: -50%
- Mano d’opera: -30%
- Area occupata: -30%
Caratteristiche Principali
- I lati di manipolazione e di saldatura sono completamente separati, evitando tempi di ozio, facendo si che tutti i robot possano raggiungere la tassa di saturazione massima (sopra al 90%)
- Mentre i robot di saldatura stanno lavorando nella parte destra della piattaforma giratoria, sul lato opposto, la parte sinistra lavora con robot per la manipolazione nel carico/scarico
- Pinze di saldatura, sistemi di chiusura, macchine integrate, robot di manipolazione, ecc. sono totalmente condivisi tra la parte destra e sinistra
- Caricamento manuale in entrambe le parti (lato destro e sinistro) sempre se è possibile, massimizzando la tassa di saturazione dei lavoratori (più del 90%)
Caratteristiche Tecniche
- Tassa di produzione fino a 66 JPH (132 pezzi per ora, 66 a destra e 66 a sinistra)
- Efficienza tecnica: 92%
- Produzione in lotti
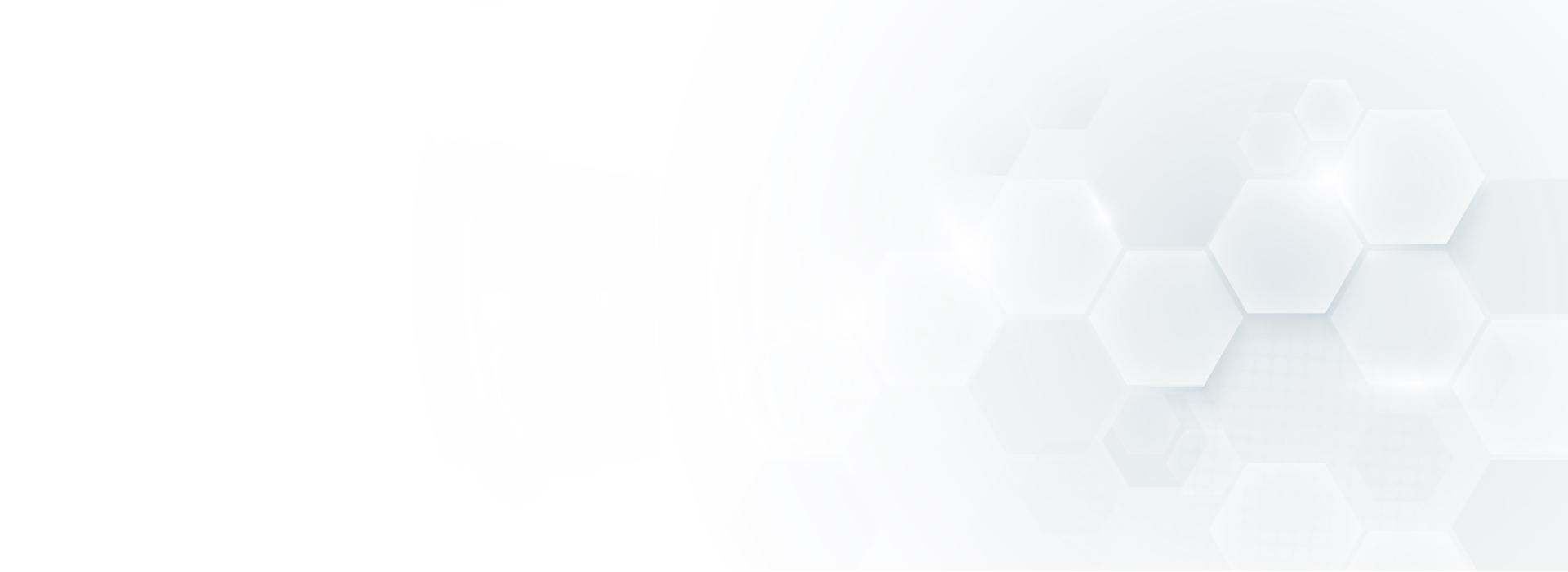
Veicoli Autonomi Guidati
I veicoli automatizzati guidati o AGV’S, garantiscono una maggior efficienza e sicurezza nello stoccare, centri di distribuzione e ambienti industriali in generale. La sua versatilità permette il trasporto di diverse tipologie di prodotto tra vari punti distinti, come tra magazzino e produzione o consegna di prodotto finale e stock.
Attraverso un sistema di lettura di codice 2D “QR code” messo sul pavimento e delle antenne che lavorano insieme, con questa programmazione si permette ai veicoli di sapere esattamente dove si incontra il proprio carico e il destino, con massima flessibilità movimento nei diversi ambienti. La sua costruzione permette l’utilizzo dia su piattaforme elevatore che su quelle giratorie permettendo all’attrezzatura di cambiare l’orientamento del prodotto tra il punto di ritirata e consegna, garantendo ancora più flessibilità’ al sistema logistico della tua azienda.
I veicoli possiedono batteria propria e la propria autonomia di carico definisce il momento di auto ricarica, senza la necessità di intervento da parte dell’equipe di logistica e manutenzione della tua azienda.
Esempio di applicazione (case study)
Il sistema di trasporto di bancali realizzato con AGV permette che i bancali di pezzi e/o prodotto siano consegnati in fianco alla linea necessaria, senza attualizzazione degli operatori.
Attraverso un sistema parametrico di traiettoria è possibile predeterminare il cammino da seguire nei corridoi della pianta, automatizzando cosi tutto il flusso di materiali a ‘lato della linea”. Utilizzando ferramenta di simulazione di flusso è possibile determinare con anticipazione se il sistema progettato riuscirà ad attendere la cadenza della linea necessaria, inclusivo simulare tutta la logistica a lato della linea.
Il carico dei bancali può essere realizzato con elevatori per mezzo di un sistema di tavoli con rulli o direttamente in forma automatizzata in linee robotizzate. Nell’area di scarico preferenzialmente si accumulano prodotti per avere un buffet di lavoro adeguato, i bancali possono anche essere messi ad un’altura ergonomica per permettere la ritirata del prodotto per l’operatore.
Caratteristiche principali
- Corso di elevazione: fino a 100 mm
- Carico utile: fino a 1000 kg
- Velocità di movimentazione: fino a 1,2 m/min.
- Livello di trasporto più basso: 350 mm
- Trattamento di superfice: pittura
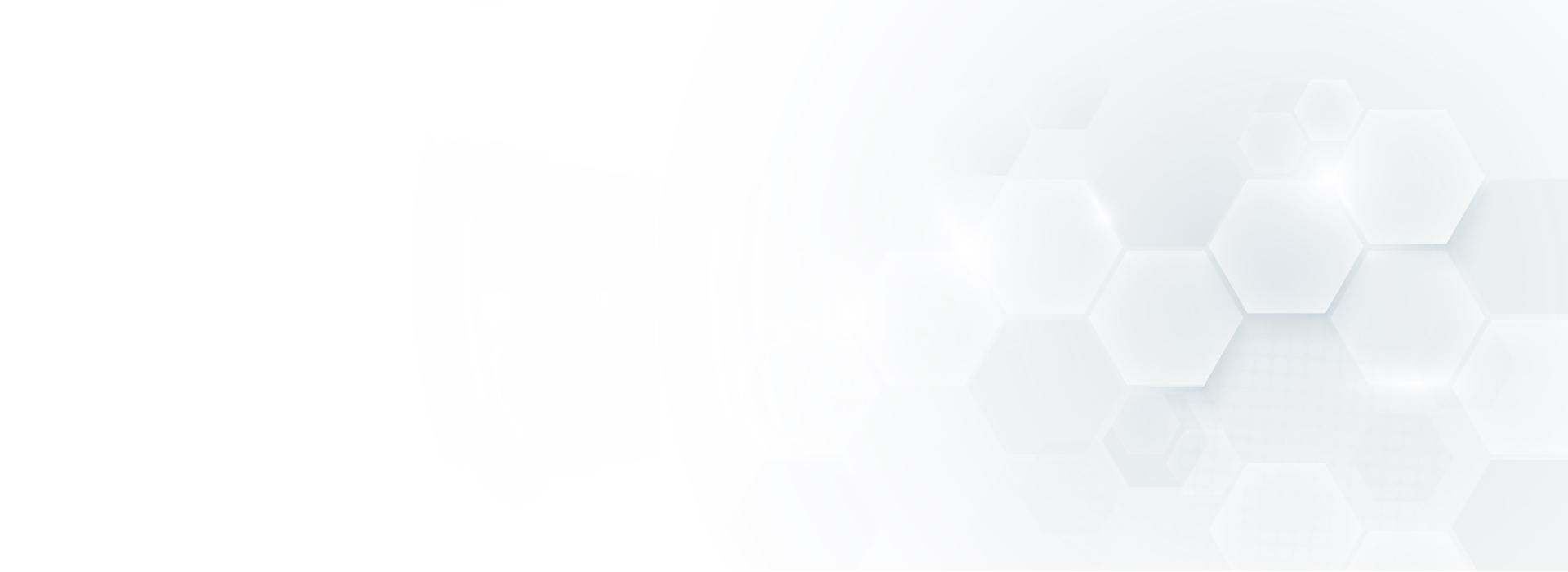
Fahrwerk - Unione tra Carrozzeria e Powertrain
Nel montaggio finale esiste una stazione dove la carrozzeria e il powertrain si uniscono di forma sincronizzata per l’assembramento dell’automobile, i fabbricanti lo chiamano di “matrimonio”. Consiste in un processo preciso, rapido e sincronizzato dove alcune dozzine di viti sono avvitate e in pochi secondi la carrozzeria finalmente si unisce al powertrain (insieme di motore e trasmissione).
Il montaggio del powertrain inizia con il montaggio di accessori del motore (tubicini e cinghie), in questo montaggio la maggior parte delle viti è realizzata in coppia controllate automaticamente.
Dopo il montaggio del motore, l’insieme powertrain è montato su una struttura specifica, che è spostata su tavoli con rotelle. Questa struttura con sopra il powertrain è portata nelle varie stazioni per il montaggio. Il powertrain è composto da motore, scatola del cambio, assi, trasmissione, scappamento, ammortizzatori e altri. La carrozzeria arriva solitamente con trasportatrici aeree con l’interno già montato.
Finalmente, in questo matrimonio, la carrozzeria sospesa viene posizionata sopra la struttura del powertrain già montato, qui si sincronizzano il trasportatore aereo con i tavoli a rotelle che trasportano il powertrain. Allo stesso tempo che le velocità di trasferimento sono sincronizzate (powertrain e carrozzeria) il tavolo di montaggio powertrain si inizia ad alzare fino ad incastrarsi con la carrozzeria. Nelle prossime stazioni vengono avvitati i vari componenti alla carrozzeria e al powertrain unendoli e trasportandoli poi insieme grazie ad una trasportatrice aerea.
Caratteristiche tecniche montaggio di motori
- Stazioni di montaggio di motori: 14 posti
- Lunghezza Trasportatrice aerea EOM di montaggio del motore: 500 m, 2 elevatori
- Velocità: da 0,5 m/s fino a 30 m/s
- Tempo di ciclo : conforme alle necessità
- Coppia con avvitatori automatici
Caratteristiche tecniche struttura di montaggio Powertrain
- Stazioni di montaggio powertrain: 14 posti
- Trasportatore di montaggio powertrain: 15 tavoli con rulli, 3 elevatori
- Velocità: da 0,5 m/s fino a 25 m/s
- Tempo di ciclo: conforme alle necessità
- Coppia con avvitatori automatici
Caratteristiche tecniche Sistema Matrimonio
- Sistema Aereo di trasporto carrozzeria: 50 metri Power&Free
- Sistema di trasporto di strutture powertrain: 2 tavoli elevatori pantografici, 10 tavoli con rotelle
- Velocità: da 0,5 m/s fino a 25 m/s
- Tempo di ciclo: conforme alle necessità
- Coppia con avvitatori automatici
- Avvitamento automatico con robot o manuale
- Controllo di accoppiamento con sistema visivo