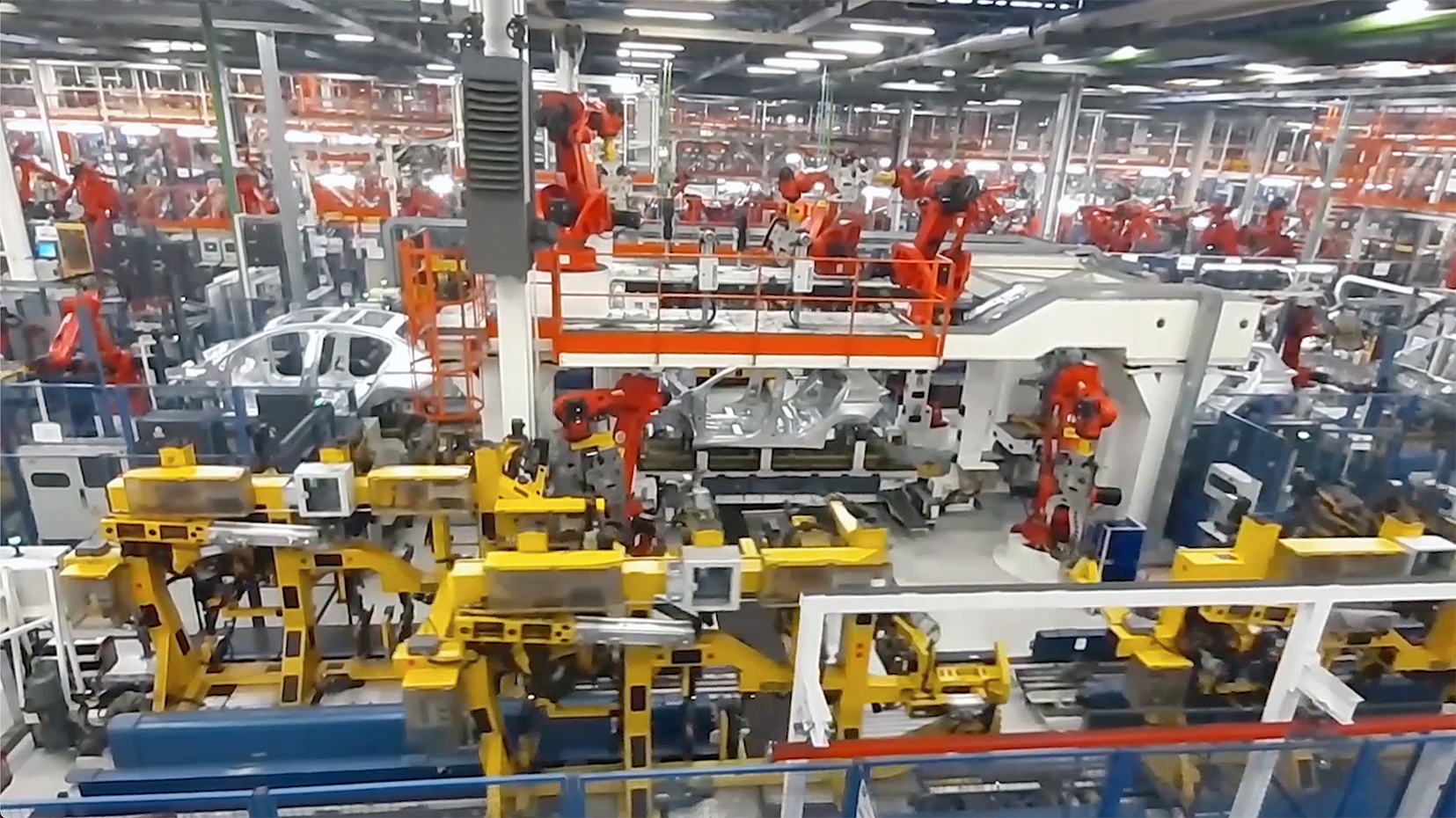
Prodotti
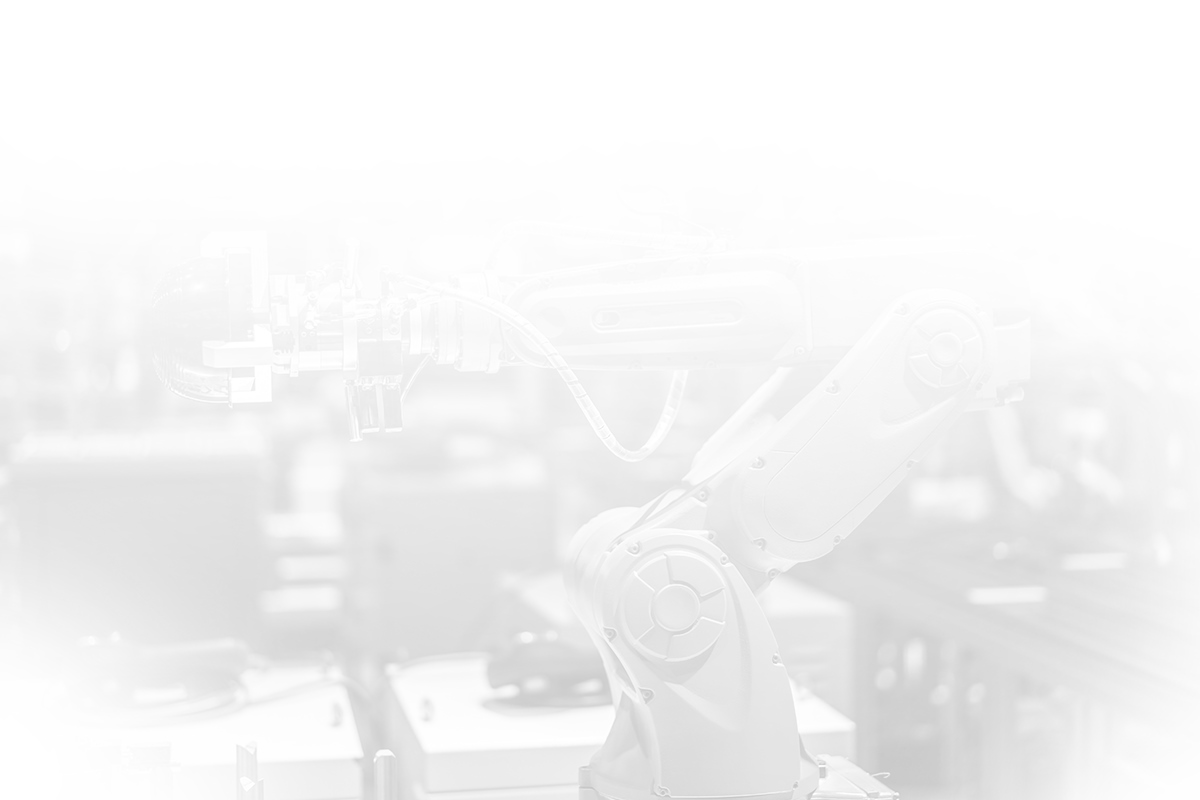
Manipolazione dei Materiali
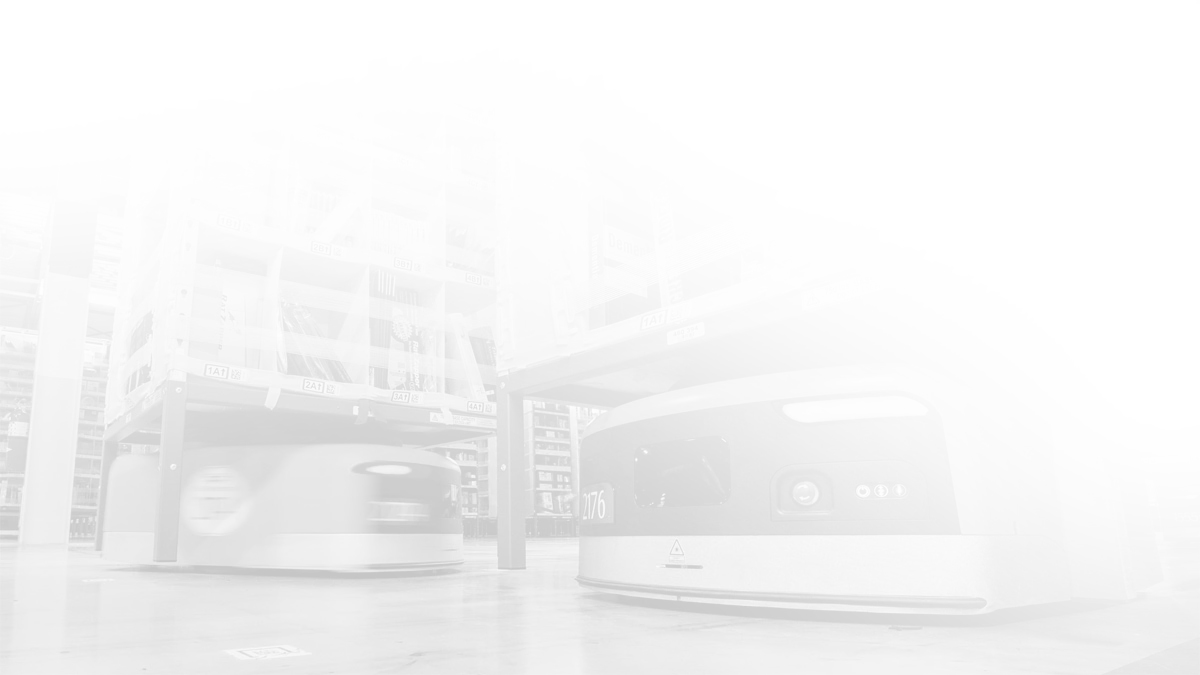
La GME ha sviluppato diversi sistemi per la manipolazione di materiali, necessari per la logistica delle linee di produzioni industriali. Trova in basso più dettagli riguardo le nostre soluzioni automatizzate di trasportatori.
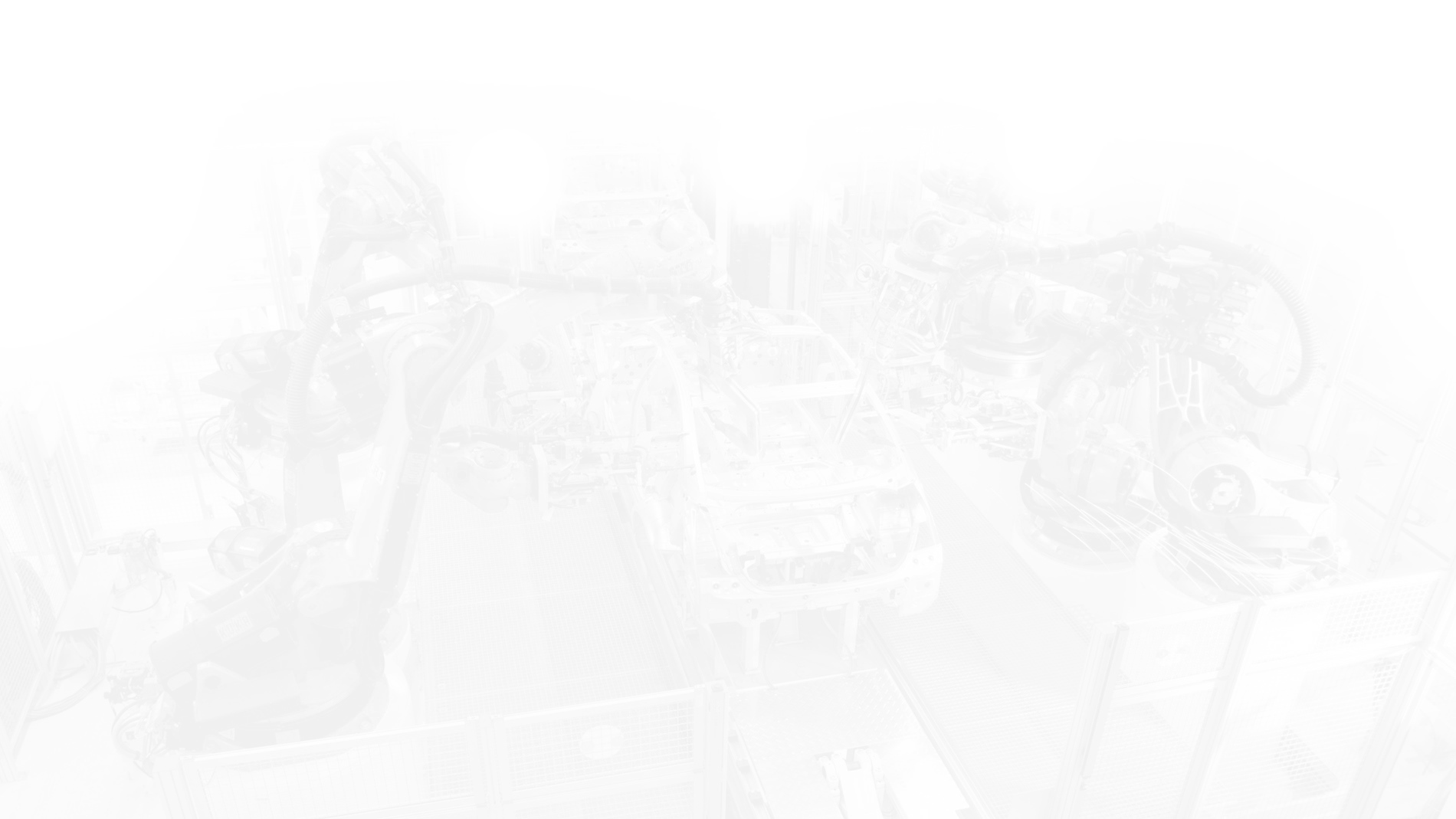
Lo Skid è un elemento essenziale della logistica di una pianta. Deve permettere il posizionamento di tutti i prodotti e deve anche permettere il buon funzionamento di tutti i trasportatori. Oltre a questo, deve garantire un posizionamento preciso dei prodotti nelle stazioni robotiche o nelle stazioni di cambio di Skid o di mezzi di trasporto.
La costruzione dentro alla tolleranza permessa e il corretto processo di fabbricazione garantiscono una Skid che avrà un comportamento stabile in tutto il processo. I modelli di Skids possono essere semplicemente per il trasporto, di trattamento superficiale utilizzati nella pittura e il tipo di Skid di geometria (per linee di saldatura).
Caratteristiche tecniche
- Dimensione massima approssimata: 8000 x 3000 x 600 (mm) (L x W x H)
- Carico massimo supportato da ogni skid approssimata: 4000 kg
- Temperature sopportate: da -10°C a 300°C
- Trattamento superficiale: Pittura/Galvanizzato
Varianti
- Acciaio inossidabile, Tag RFID, chiusure per prodotti, normalizzazione per vibrazione o per temperatura dopo la saldatura
Tavoli di rulli motorizzati, anche chiamata di Power Roller Beds, sono la base della logistica basata su sistemi di trasporto con Skids.
Progettate per essere modulari, semplici e con alta disponibilità di funzionamento, il sistema è adeguato principalmente per trasporto e manipolazione di carrozzerie. Altamente flessibile, possono essere istallati su cavalletti su qualsiasi pavimentazione, su elevatori, shuttles e altre attrezzature delle linee di trasporto di Skids.
Con un design standard, possono essere create varianti dal modello padrone in accordo con le esigenze specifiche per ogni processo e cliente.
Caratteristiche tecniche
- Dimensioni massime approssimativamente: 8000 x 3000 x 2000 (mm) (L x W x H)
- Carico massimo per ogni Skid approssimativamente: 4000 kg
- Velocità di trasporto: da 15 a 100 m/min
- Cadenza approssimativa: 90 cicli per ora
- Rulli motorizzati per catene sincronizzanti o catene metalliche
- Rulli vulcanizzati o di acciaio in accordo con le necessità del procedimento
- Trattamenti superficiali: pittura/ galvanizzazione
Varianti
- Quantità di rulli per ogni tavolo, struttura in acciaio inox inossidabile, trazione per catene utilizzate ad alta temperatura, coperchi di protezione per permettere il lavoro o il passaggio di addetti ai servizi, velocità variabile dei rulli, guide laterali, battente di sicurezza pneumatica, centralizzatore di posizione di stop pneumatico.
Attrezzatura utilizzata nelle linee di trasporto di skid per realizzare curve in accordo con il layout. Possono anche essere utilizzate per invertire l’orientamento del coordinato skid/carrozzeria in una linea di trasporti della skid. I tavoli giratori possono essere costruiti con l’asse giratoria concentrico o eccentrico.
Caratteristiche tecniche
- Dimensioni massime approssimativamente: 8000 x 8000 x 2000 (mm) (L x W x H)
- Carico massimo per ogni Skid approssimativamente: 4000 kg
- Velocità di trasporto: massima 50 m/min
- Velocità di rotazione: 15 m/min (6 a 8 secondi)
- Rotazione: fino a 360°
- Cadenza approssimativa: 90 cicli per ora
- Rulli motorizzati per catene dentate
- Rulli vulcanizzati o di acciaio in accordo con le necessità del procedimento
- Trattamenti superficiali: pittura/galvanizzazione
Varianti
- Giro concentrico o eccentrico, struttura in acciaio inox inossidabile, trazione per catene ad alta temperatura, coperchi di protezione per permettere di lavorare o passare agli operatori, velocità variabile dei rulli, guide laterali, sistema anti-caduta, driver di accensione a bordo o in pannelli
Rullo trasportatore utilizzato per trasferire un skid da una linea all’altra. Il Shuttle possiede un tavolo di entrata e uno o più tavoli di uscita cosi riesce a dividere il flusso d’accordo con le necessità.
Caratteristiche tecniche
- Altezza di trasporto: da 400 a 800 mm
- Carico utile: da 20 a 2000 kg (fino a 4000 kg per sistemi di manipolazione di skid)
- Velocità di dislocamento: fino a 24 m/min per un periodo di ciclo ideale
- . Traino a rulli, tavoli giratori, traino a catene (o forcelle telescopiche) montate sopra allo stesso sistema
- Trattamento superficiale: pittura/galvanizzazione
Varianti
- Copertura, supporti discensori aggiustabili, sistema di posizionamento di codice a barre, registratore/lettore RFID, raccolta di energia per barriere o induzione senza contatto invece di catene di traino.
Il sistema Cross Transfer & Mesa Pop-Up, sono usati quando il tuo flusso è diviso in più flussi o mescolato in altri flussi. La carica e ‘quindi trasferita da una mesa Pop-Up all’altra per mezzo di catene di plastica o metallo, permettendo cosi un miglior ciclo che lo Shuttle Transfer oltre che di accumulo di prodotto.
I tavoli ad elevazione Pop-Up, o mesa di dislocamento sono essenziali quando il tuo flusso deve essere accumulato e deviato a 90°. Lo skid o pallet è trasferito da un trasportatore di catena per un rullo trasportatore o vice versa.
Caratteristiche tecniche
- Altezza di trasporto : da 400 a 800 mm
- Corso: fino a 50 m
- Carica utile: da 20 a 2.000 kg (fino a 4.000 kg per sistemi di manipolazione di skid)
- A bordo: un rullo trasportatore , un trasportatore a catene o forcelle telescopiche
- Trattamento superficiale: pittura/galvanizzazione
Varianti
- Azionamento doppio per backup, copertura, supporti di sensori regolabile, sistema di posizionamento di codice a barre, registratore/ lettore RFID, raccolta di energia per barometri o di induzione senza contatto invece di corrente di traino
Gli Elevatori a Colonna sono utilizzati quando la logistica di produzione ha bisogno di cambiare livello, permettendo di dislocare la merce in verticale. Nei casi in cui il sistema di trasporto Skid/EOM è impiantato su vari livelli, gli elevatori permettono un movimento verticale della merce.
Caratteristiche tecniche
- Corso dell’ elevatore: da 400 a 20.000 mm
- Carica utile: da 20 a 5000 kg
- Velocità di elevazione: da 10 a 60 m/min
- Altezza di manifattura nella posizione bassa 400 mm
- Rullo trasportatore a bordo
- Trasportatore a catena a bordo
- Trasportatore EOM a bordo
- Tavoli con rulli energizzata
- Forcelle telescopiche
- Accensione con energia elettrica o pneumatica
- Principio di elevazione: cavi di acciaio, guide o catene
- Trattamento superficiale: pittura/galvanizzato
Variazioni
- Catena di plastica, catena di metallo, accensione doppia per permettere la reversione, coperture, supporti di sensori regolabili, sistema di posizionamento di codici a barre, registratore/lettore RFID, raccolta di energia per barometri ad induzione senza contatto invece di catena di traino, chiusura di sicurezza
I tavoli di elevazione articolati a forbice o tavoli pantografici sono indicati principalmente quando il tuo flusso ha bisogno di un cambio di livello nello stesso pavimento. I tavoli pantografici possono essere applicate in linea di processo automatizzato o manuale.
Caratteristiche Tecniche
- Corso di elevazione: da 400 a 2000 mm
- Carica utile: fino a 3000 kg
- Velocità di elevazione: da 4 a 20 m/min
- Livello di trasporto più basso: 400 mm
- Trasportatori a bordo: tavolo di rulli, trasportatore a catena o forcelle telescopiche
- Energia per accensione: idraulica o elettrica
- Trattamento superficiale: pittura/galvanizzato
Varianti
- Coperchi, supporti per sensori aggiustabili, grata di protezione tubolare (tutta l’estensione verticale dell’elevatore), doppio motore, sistema di posizionamento per encoder o sensori, registratore/lettore di RFID, chiusura di sicurezza
Disegnato per movimentare lentamente il prodotto in ritmo costante facilitando la manipolazione del prodotto, può trasportare prodotti o operatori.
- Costruiti in acciaio o in materiale plastico offrono condizioni di ergonomia e sicurezza per le operazioni manuali
- Sono attrezzature ideali per montaggio finale o linee di rifiniture manuali
Caratteristiche Tecniche
- Lunghezza del trasportatore: fino a 150 metros
- Carico utile per ogni tappa di lavoro: Massimo 4000 kg
- Velocità: da 0,5 m/s fino a 10 m/s
- Tempo durata ciclo: conforme alle necessità
- Trattamento superficiale: struttura dipinta, altri elementi dipinti secondo le esigenze ( pitturato/galvanizzato, in linea, ecc.)
Varianti
- Pit, coperchi, reti di sicurezza, velocità variabile, pulsanti di chiamata, IHMS, Lettore di codice a barre, Tunnel di illuminazione per ispezione visuale, altezza di operazione variabile in accordo con le necessità di ergonomia
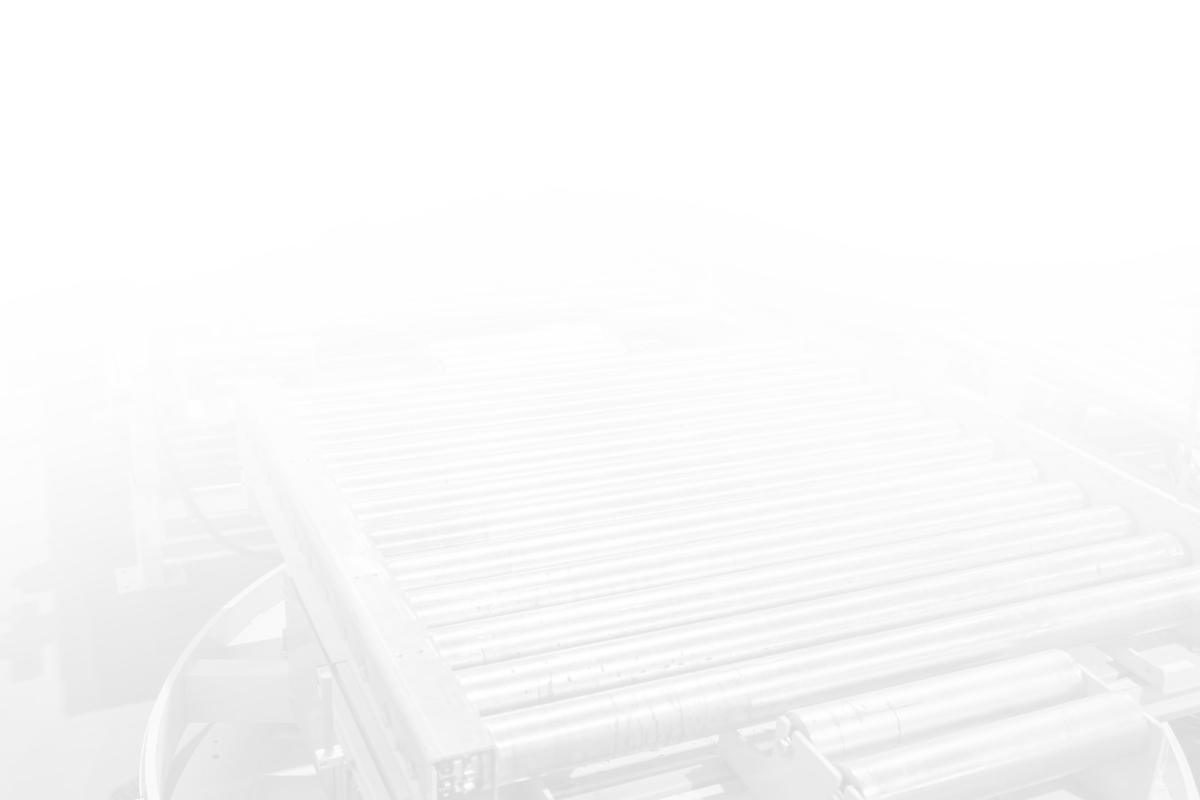
Lifter Roller Tables
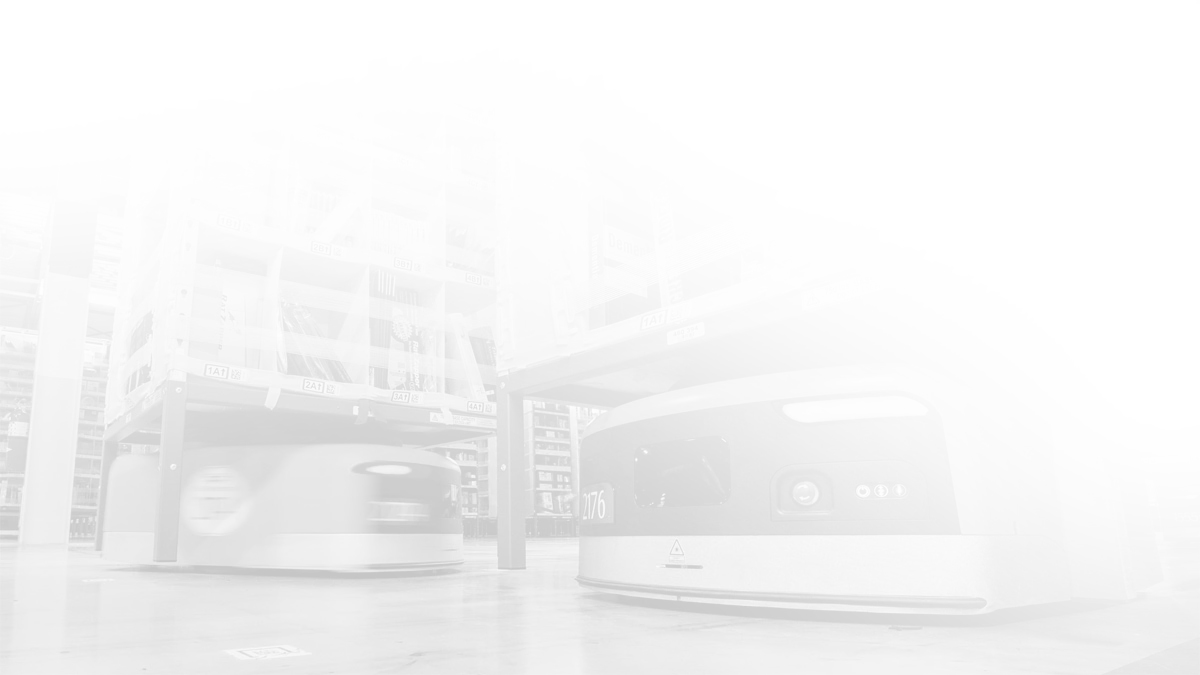
I tavoli di Elevazione di Fuso GME permettono il posizionamento di congiunti skid/carrozzeria nelle stazioni di una linea. Le stesse sono accessoriate con due sistemi basici per effettuare questo compito:
- Sistema di traslazione
- Sistema di elevazione
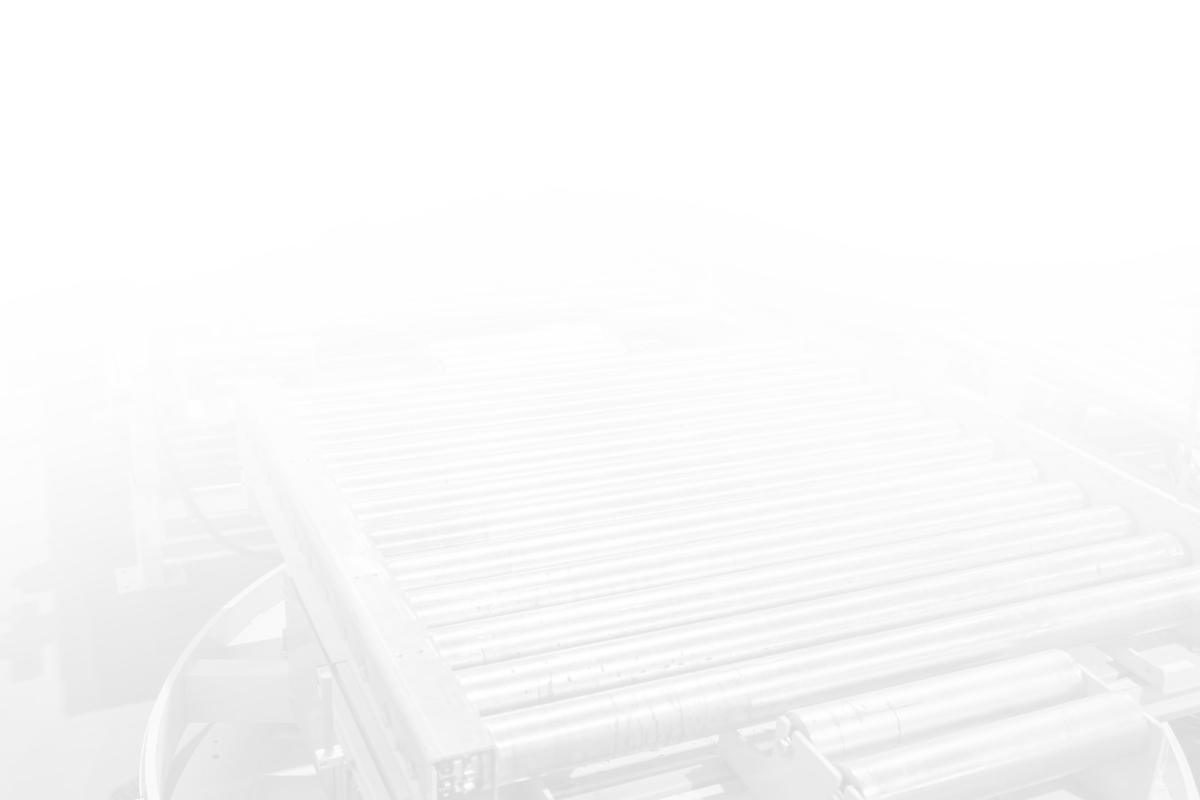
Il sistema di elevazione è composto da due torri parallele che hanno viti a sfere sincronizzate per mezzo di cardam accoppiato con un accensione motorizzata. L’insieme di elevazione è dimensionato in accordo con le necessità del prodotto e velocità richieste dal processo.
Per quanto riguarda la traslazione tra le stazioni dell’ unione skid/carrozzeria è utilizzato il concetto di tavoli con rulli con ruote guida. Le ruote guida permettono che lo spostamento sia fatto ad una velocità fino a 120m/min.
Il sistema è adattabile alle differenti misure di skid/carrozzeria in accordo alle necessità pratiche dell’istallazione, potendo cosi essere applicate in diverse stazioni e applicazioni.
Caratteristiche Principali
Con base nell’esperienza della GME, sommata allo scambio di esperienza con le aziende dei clienti e teste realizzati, sono stati impiantati considerevoli miglioramenti nel prodotto per aumentare il disimpegno dell’attrezzatura. La GME ha istallato intorno alle 80 attrezzature in Brasile, Argentina, Italia, dall’anno 2017.
Qualche differenza in distacco:
- Attrezzatura montata in “base unica”(unico sistema di riferimento) che permetto il montaggio rapido in ambiente industriale
- attrezzatura consegnata montata e regolata, lasciando fuori solo l’istallazione e funzionamento. Non serve prendere le misure con laser per l’istallazione
- Sistema di guida doppia che aumenta la vita utile dei vari componenti per l’elevazione. Le torri di elevazione possiedono un sistema di guide lineari che lavorano insieme alla vite a sfere per trasmettere la movimentazione dell’elevazione. Da un altro lato, i tavoli con rulli possiedono un sistema di rulli di acciaio che guidano il tavolo nel movimento verticale. Di questa forma, il sistema di guide del tavolo, più robusto, assorbe forze che derivano dalla decelerazione generata dal congiunto skid/carrozzeria nella dinamica generale del funzionamento dell’attrezzatura
- L’attrezzatura è integrata con componenti commercializzati, permettendo la sostituzione dei componenti equivalenti, in caso servi
- Sistema di catena doppia per la trasmissione di forza motore e nelle catene di rulli 2-3
- Sistema di centralizzazione di skid per centralizzare la merce e Stopper di sicurezza per proteggere stazioni manuali vicine
- Il movimento dell’attrezzatura è controllato da motori riduttori a maglia chiusa (usando encoders) o per mezzo di servomotori per ottenere più velocità’
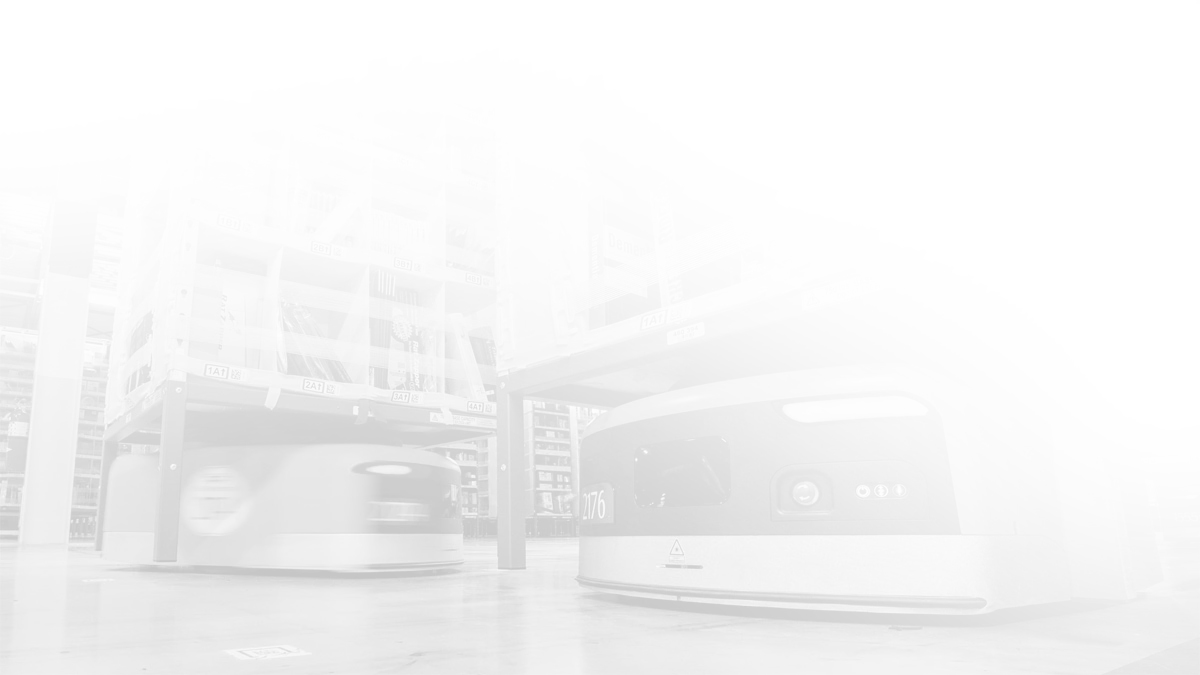
Logistica
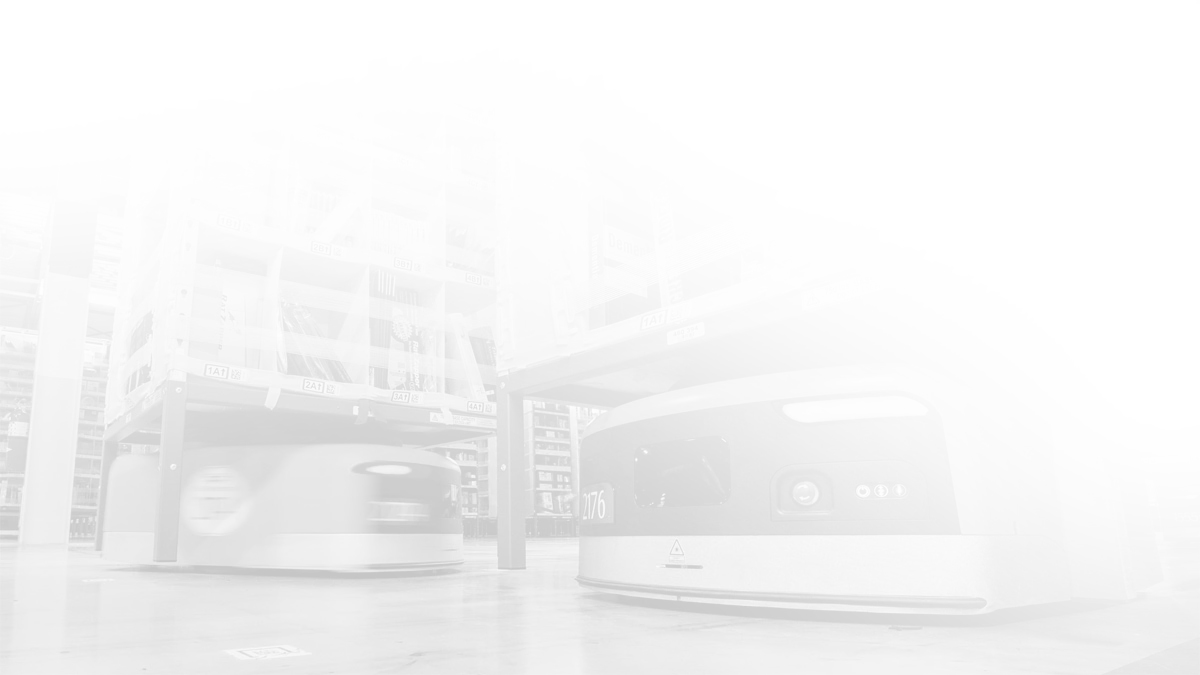
Insieme al Gruppo EFORT WFC, la GME ha sviluppato diversi sistemi logistici, necessari per il carico e scarico automatico di pezzi della linea di produzione. Le soluzioni logistiche devono essere precise, affidabili, di facile uso e buona manutenzione per rispondere ai requisiti delle fabbriche di produzione altamente automatizzata.
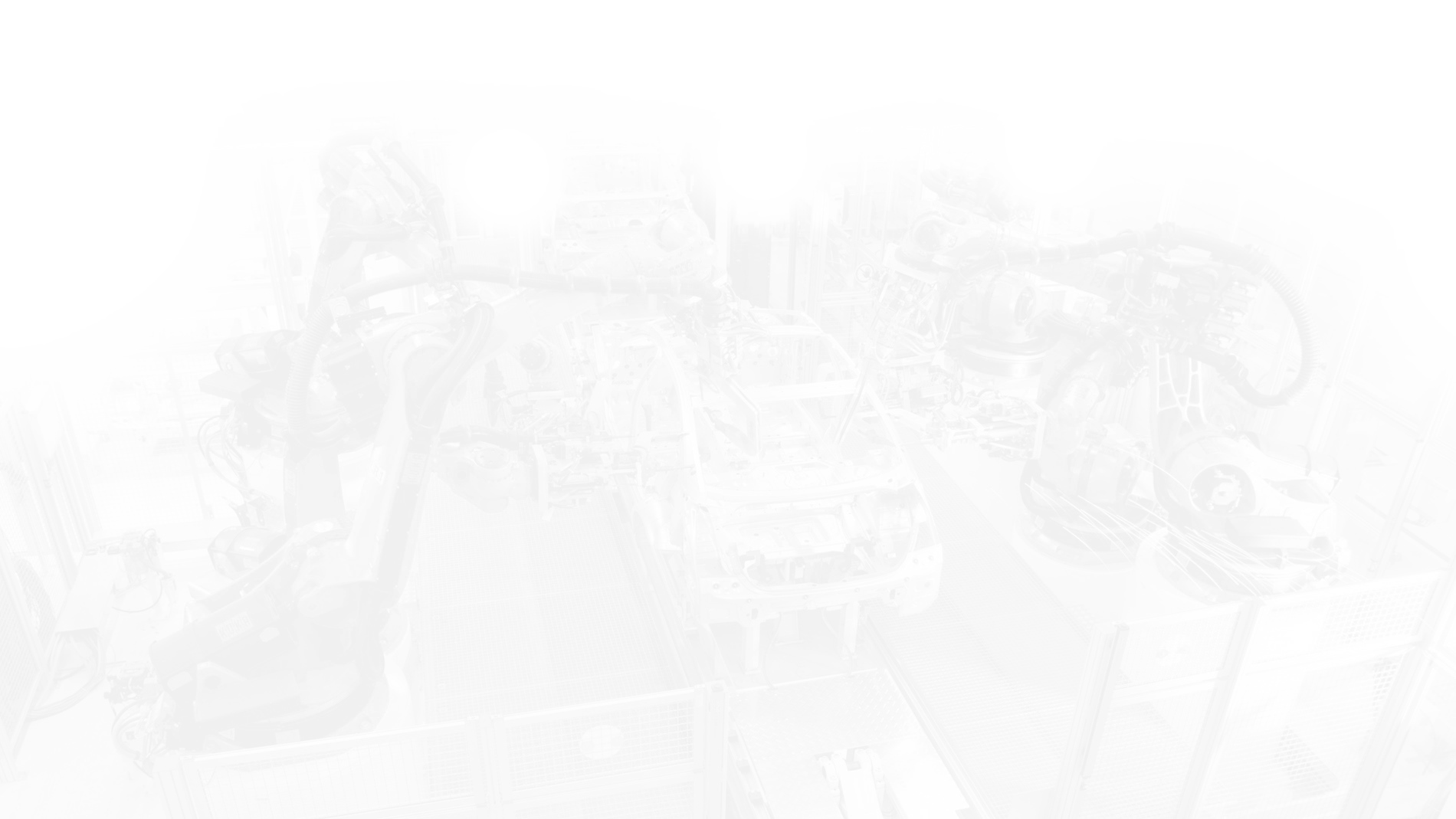
Sistema rotativo di carico/scarico, per sostituzione rapida di bancali pieni per quelli vuoti, durante la produzione (senza perdere tempo nel ciclo di produzione).
Il montacarichi possiede 2 movimenti, il primo verticale (per separare il bancale dal carrello che lo trasporta), più uno rotativo (per sostituzione del bancale).
L’operatore è facilitato durante le operazioni di carico/scarico grazie alle sue guide a rotelle, che permettono una rapida sostituzione del bancale. Quando il bancale è nel lato interno della linea di produzione, è sempre controllato grazie ad un sistema centralizzato, al fine di garantire la ripetizione necessaria richiesta dal suo robot per le operazioni di carico/scarico automatico.
Sistema di montacarichi con apertura orizzontale, carico/scarico, per una sostituzione di bancale pieni per quelli vuoti, durante la produzione (senza perdere tempo nel ciclo di produzione).
Le porte di protezione si aprono e chiudono alternatamente al fine di mantenere sempre separate le varie aree di lavoro del robot con le aree dell’operatore, che realizza le operazioni di carico/scarico del bancale nel lato opposto. In questo modo le condizioni di sicurezza sono garantite durante tutto il ciclo.
Sistema di carico/scarico con movimento verticale e ri-circolazione dei bancali. Sostituzione rapida di bancale pieni per quelli vuoti durante la produzione senza far perdere tempo al ciclo di produzione e economizzando spazio al lato del carico. Si tratta di una soluzione particolarmente adatta in caso di spazio ridotto tra le linee di produzione.
Sistema di montacarichi con apertura lineare verticale (porta doppia), buffer superiore e piattaforma di accesso per la manutenzione. Carico/scarico di bancali pieni per quelli vuoti con muletto e durante la produzione senza perdita di tempo del ciclo di produzione. Soluzione più semplice e compatta adatta principalmente a bancali molto pesanti e difficili da movimentare manualmente.

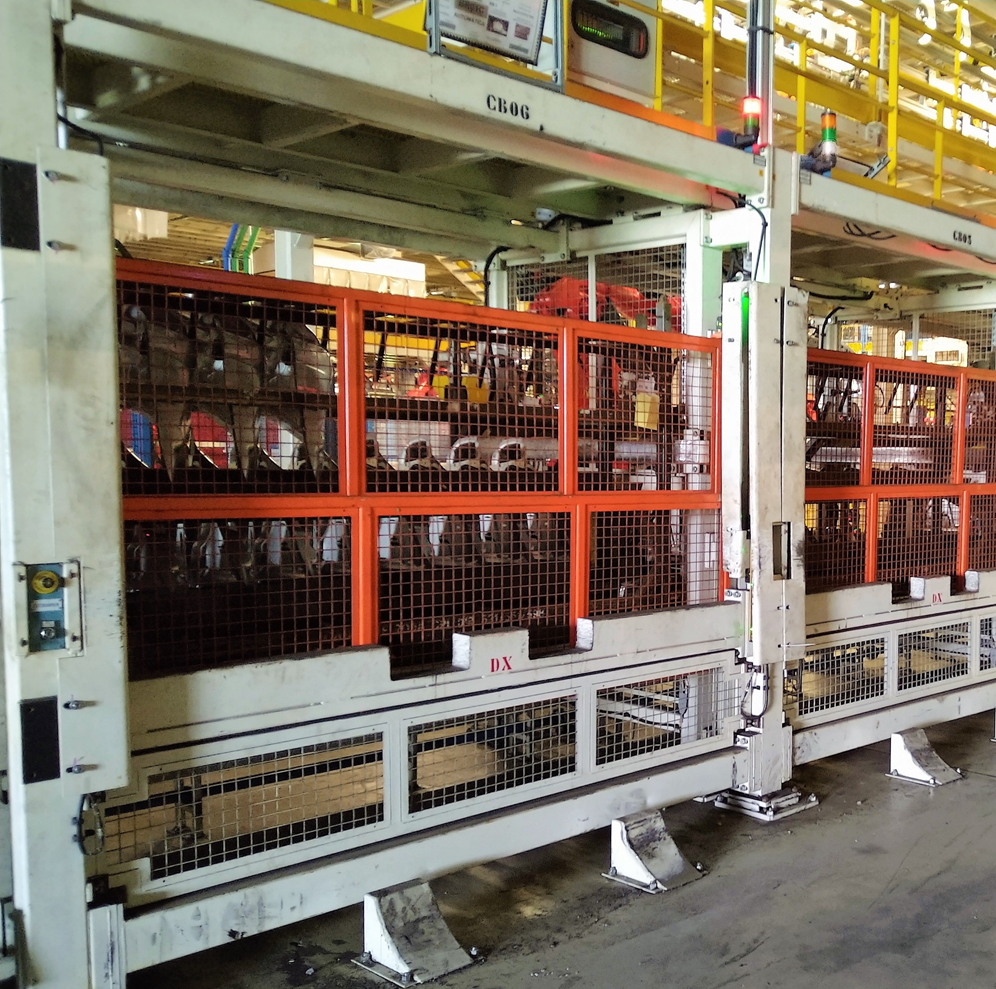
Sistema di montacarichi con ricarica manuale e consumo automatico, con movimento giratorio automatico. Questo sistema è proposto come alternativa al classico APC (Automatic Pallet Conveyor) riducendo lo spazio a lato della linea di produzione e diminuendo significatamene i costi rispetto l’uso di un rullo trasportatore tradizionale.
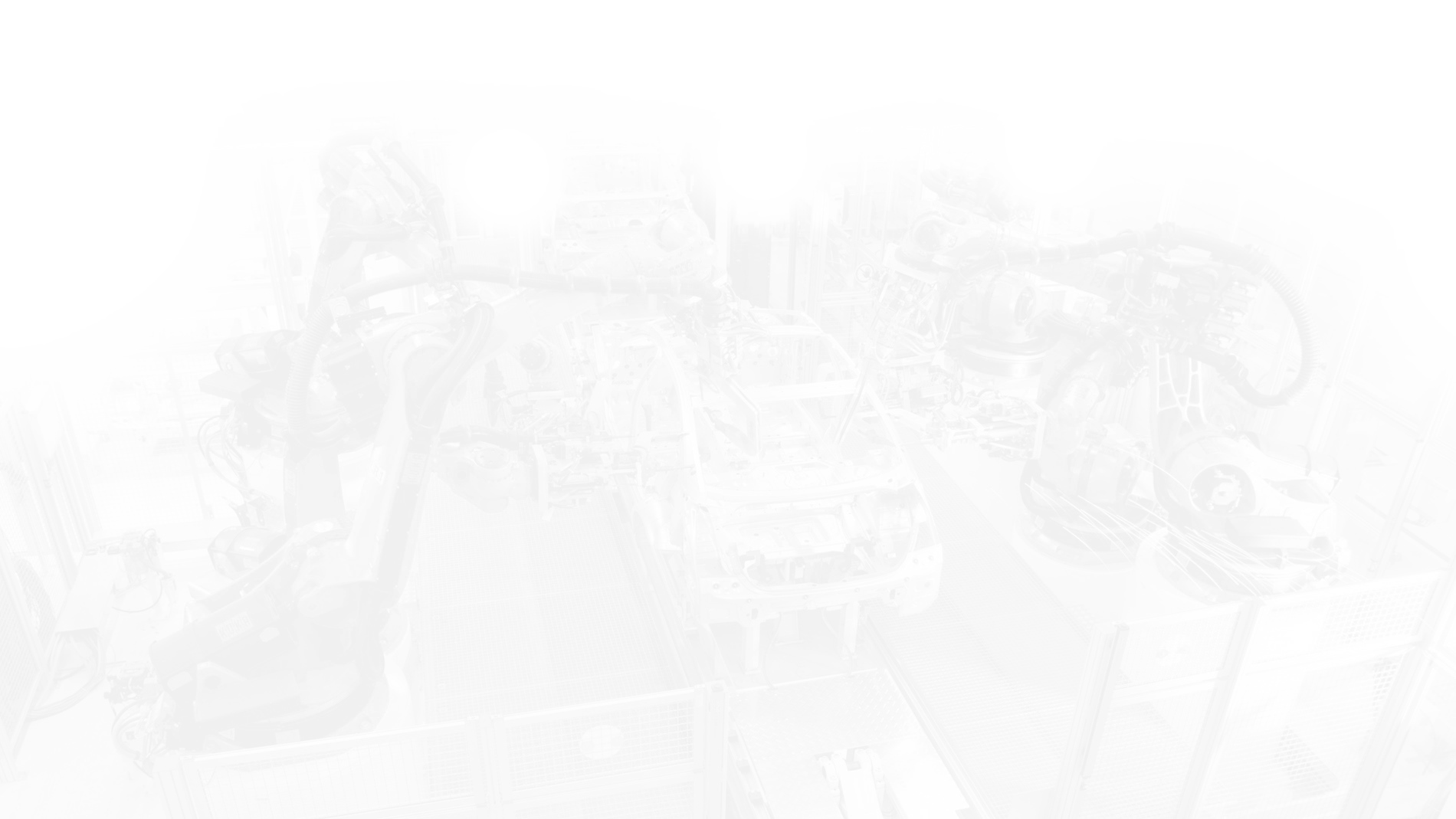
Hemming Systems
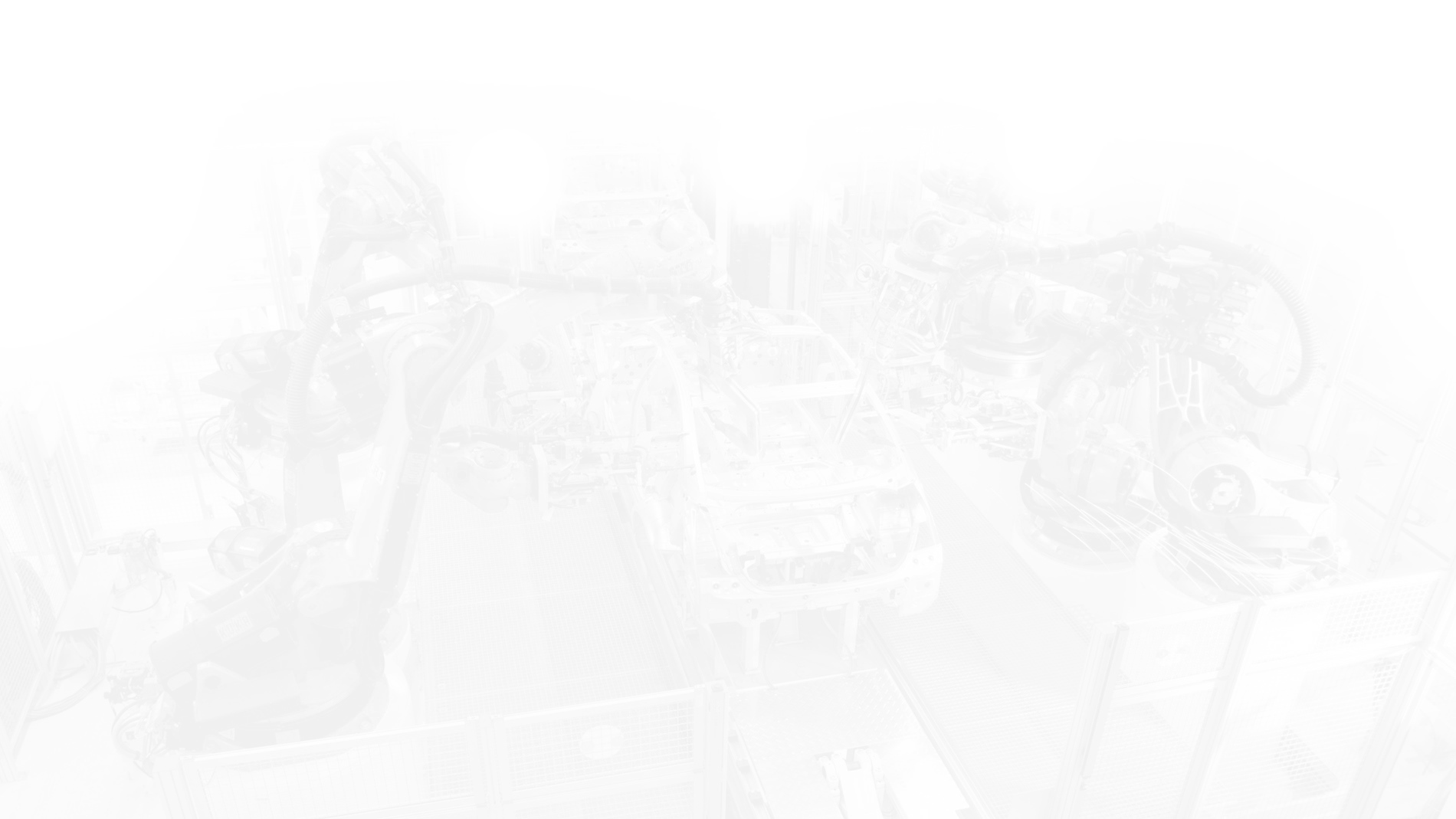
La tecnologia Table della GME è basata su un sistema automatico, includendo un insieme di elementi elettronici che compongono la macchina di imbottigliamento. Questo sistema può essere usato tanto con pezzi di acciaio tanto con pezzi di alluminio. La tecnologia del Table Top Hemming offre una miglior qualità del prodotto, con meno necessità di spazio e tempo di ciclo ridotto.
Il sistema robotico di imbottigliamento roller hemming consiste in un robot industriale standard integrato con una testata di Hemming, offrendo una soluzione molto flessibile. La testata della Hemming è composta da un corpo centrale, con guide con rulli che sono progettate in accordo con la geometria del prodotto del cliente. Si tratta di un sistema più semplice rispetto alla versione Table Top (più adatta per quelle linee di produzione con volumi di produzione elevati), offrendo una maggior flessibilità. La tecnologia di roller hemming può essere usata sia con elementi di acciaio che di alluminio.
Le testate STD GME di Roller Hemming, possiedono una combinazione di rulli ad alta resistenza, che unite si adattano a diverse caratteristiche dei prodotti dei nostri clienti.
Possiede una facile manutenzione, istallazione e adattabilità con tutti i robot utilizzati in questo processo.
Oltre a questo, i rulli di imbottigliamento sono movimentati direttamente grazie all’attrito con i pezzi con cui entra in contatto, evitando quindi la necessità di una fonte di alimentazione. Questa caratteristica permette allestimento esterno per i robot, riducendo cosi lo spazio occupato diminuendo i costi.
Sistema STD GME per correggere l’angolo delle alette perimetrali, quando quest’ultimo rappresenta un angolo eccessivamente aperto. Questo sistema ha come obbiettivo di ridurre l’angolo di apertura delle alette quando è superiore ai limiti consentiti dal sistema di imbottigliamento Table-top generando un angolo di piega per mantenere la tolleranza nel processo. Si tratta di un sistema elettro-pneumatico adatto sia per elementi di acciaio sia di alluminio offrendo una miglior qualità del prodotto finito, adatta a linee di produzione con spazio limitato e volume di produzione elevato.
L’operazione di pre-imbottigliamento può essere realizzato utilizzando anche un rotolo di imbottigliamento specifico o anche i principi dell’unità elettro-meccanica.
Sistema STD GME per piegare le alette in zone di difficile accesso (angoli acuti del prodotto). Questo sistema ha l’obbiettivo di preparare queste regioni per il processo di imbottigliamento roller hemming o Table Top.
Si parla di un sistema elettro-pneumatico adatto sia per elementi di acciaio si di alluminio, offrendo una miglior qualità del prodotto finale, adeguato a linee di produzione con spazio limitato e volume di produzione elevato.
La GME sta sempre cercando nuove soluzioni e sviluppi tecnologici disponibili nel mercato per migliorare ogni giorno i nostri processi di sviluppo di linee e attrezzature. Con questa visione, incorporiamo un software che direziona il nostro Team verso una miglior performance negli sviluppi dei dispositivi della hemming come per quelli Table-Top e quelli Roller Hemming.
Questo software permette di definire e ottimizzare facilmente l’operazione hemming, identificando e simulando le deformazioni nelle pieghe del prodotto e tensioni generate nella fase di progettazione, creando anche le geometrie della ferramenta necessaria per la simulazione. Con questo software, i processi hemming con rulli, utensili e nel Table-Top possono essere progettati di forma efficiente. Dipendendo dalla fase di processo di sviluppo del prodotto, il software supporta due casi di applicazioni, l’analisi iniziale di imbottigliamento e analisi di imbottigliamento avanzata.
Vantaggi
- Definizione dei processi di imbottigliamento per soddisfare i requisiti di qualità e di costo
- Primi studi di fattibilità e validazione finale
- Identificazione dei difetti tipici di imbottigliamento
- Previsione del ritorno elastico nell’assieme assemblato dopo di imbottigliamento
Caratteristiche principali
- Definizione di processo di imbottigliamento con rulli, utensili e con Table-Top
- Valutazione anticipata di vari concetti di imbottigliamento – in caso di applicazioni di studio iniziali di imbottigliamento
- Valutazione finale di concetto di imbottigliamento – in caso di applicazioni di studio di imbottigliamento avanzato
- Definizione della geometria e cinematica degli utensili
Principali caratteristiche
- 45° attrezzi di hemming, lavorando perpendicolarmente al flangia
- 90° attrezzi di hemming, lavorando perpendicolarmente al flangia
- Sistema elettro-meccanico
- Numero basso di componenti
- Facile manutenzione
- Tempo di ciclo hemming (escludendo carico/scarico dei pezzi): da 18seg fino a 33seg, Dipendendo dal sistema, (con il suo servo-motore) e tipologia del prodotto del cliente
- Pressa piatta: azionamento pneumatico o elettromeccanico
- Unità istallate del mondo fino ad oggi: 640
- Più grande capacità di produzione per unità : 5.500.000 (porte)
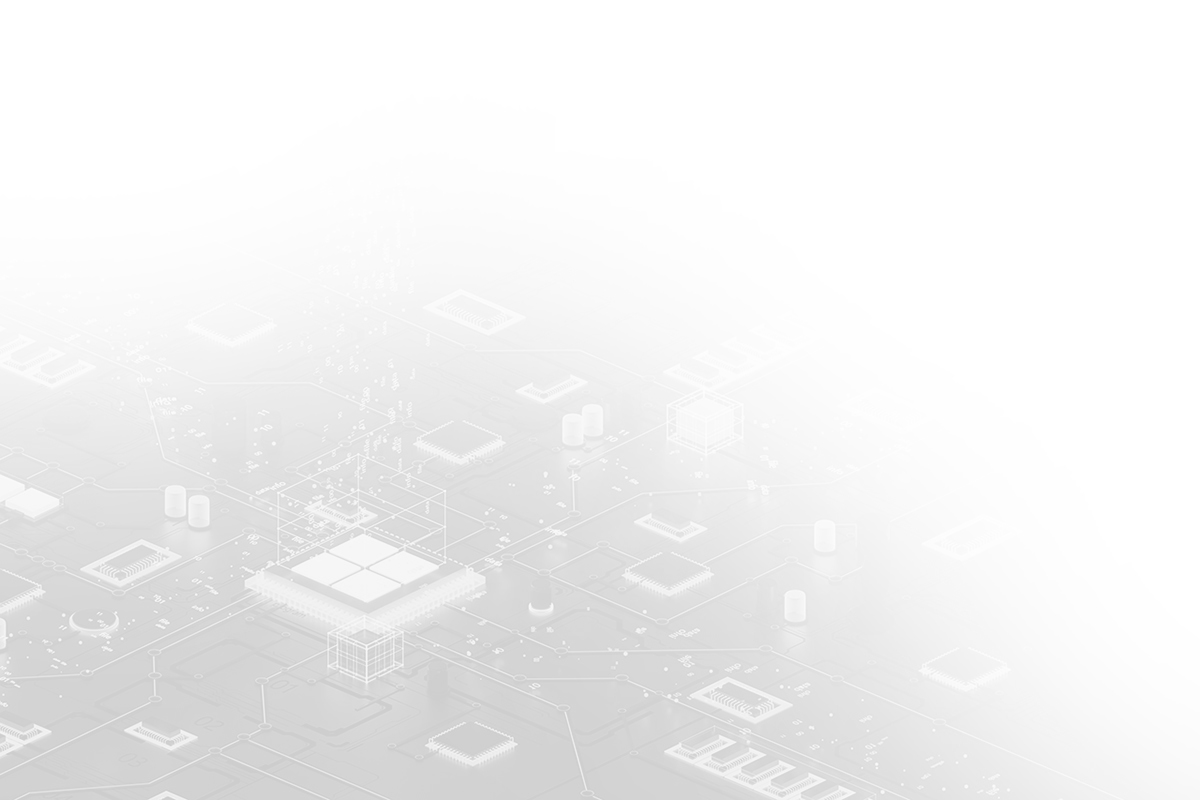
Geo Framing (CUBO)
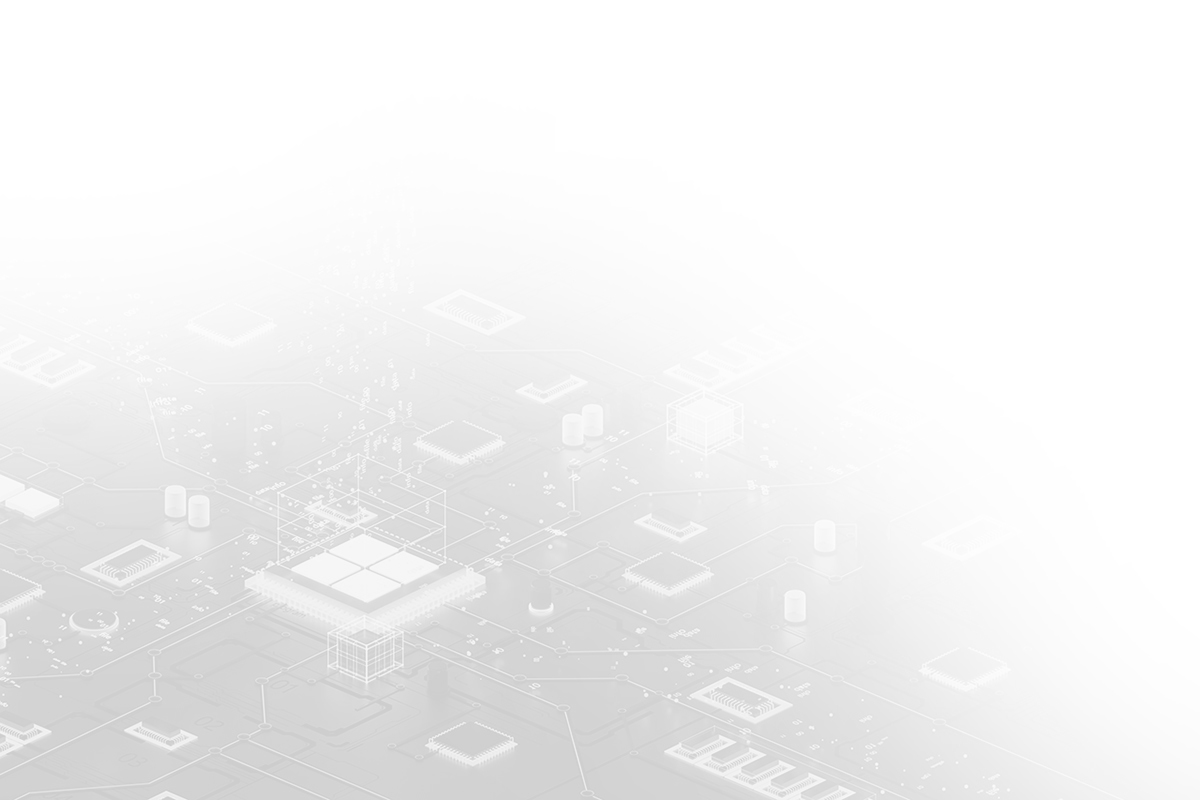
Il Geo Framing è una delle operazioni più importanti e cruciali in tutta la Body Shop, dove le parti inferiore, le laterali e le traverse della carrozzeria sono saldate insieme. La GME, unita con la succursale italiana OLCI Engineering, sviluppò una. Nuova soluzione patentata e chiamata di “CUBO” dovuto ala sua forma che ricorda l’omonima forma geometrica.
Principali caratteristiche
- Flessibilità fino a 4 modelli (dovuto ai limiti di larghezza dell’area, generalmente 20 metri al massimo)
- Reperibilità molto alta garantita dal sistema di blocco pneumatico lungo gli stampi e del telaio chiuso
- Sostituzione di modelli in 10 secondi (durante il trasferimento dello skid dall’operazione precedente a quella successiva) permettendo un’alta tassa di produzione nel modo di mescolaggio aleatorio
- Capacità di produzione fino a 60 JPH
- Alta densità punti di saldatura (fino a 12 robot), dovuto alla programmazione off-line molto precisa
- Robot sospesi sono installati sotto un portico (completamente isolato dalle stazioni di inquadramento) per prevenire vibrazioni che affetterebbero la qualità finale del prodotto (causato dal movimento dei robot) durante la saldatura a punti
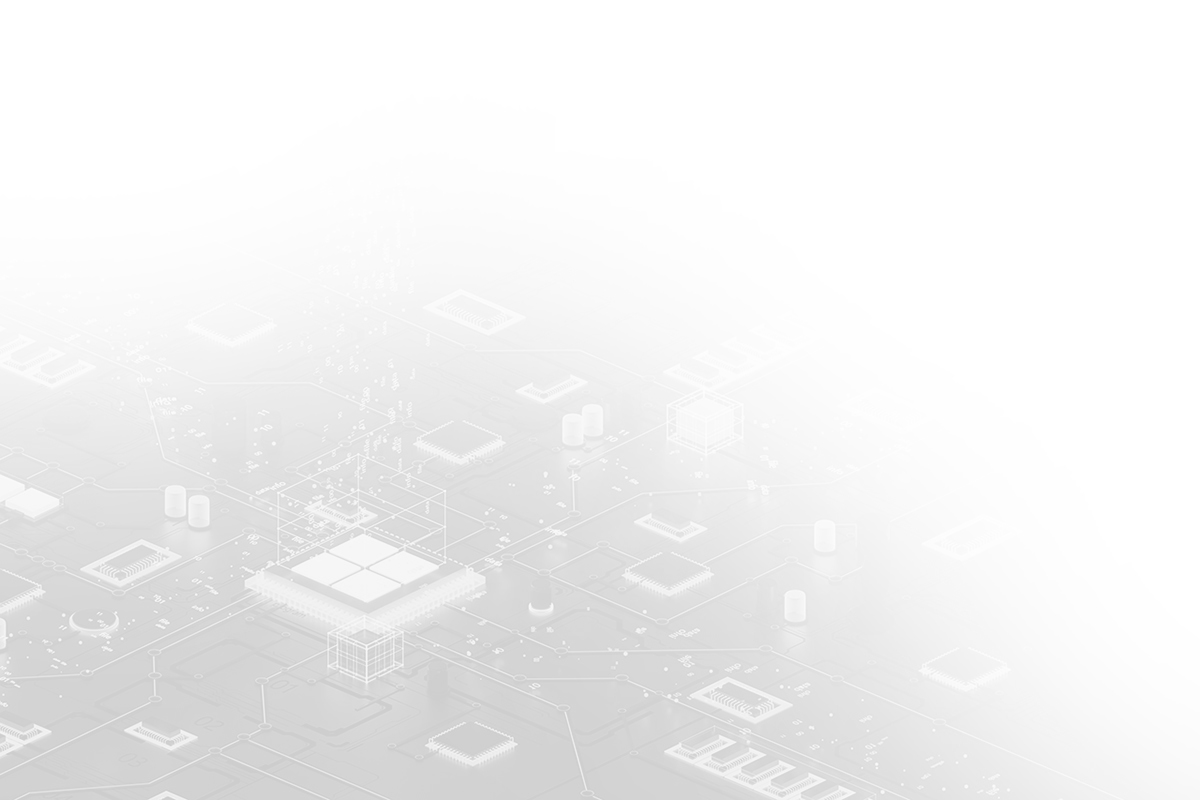
Sistemi di Trasporto EOM
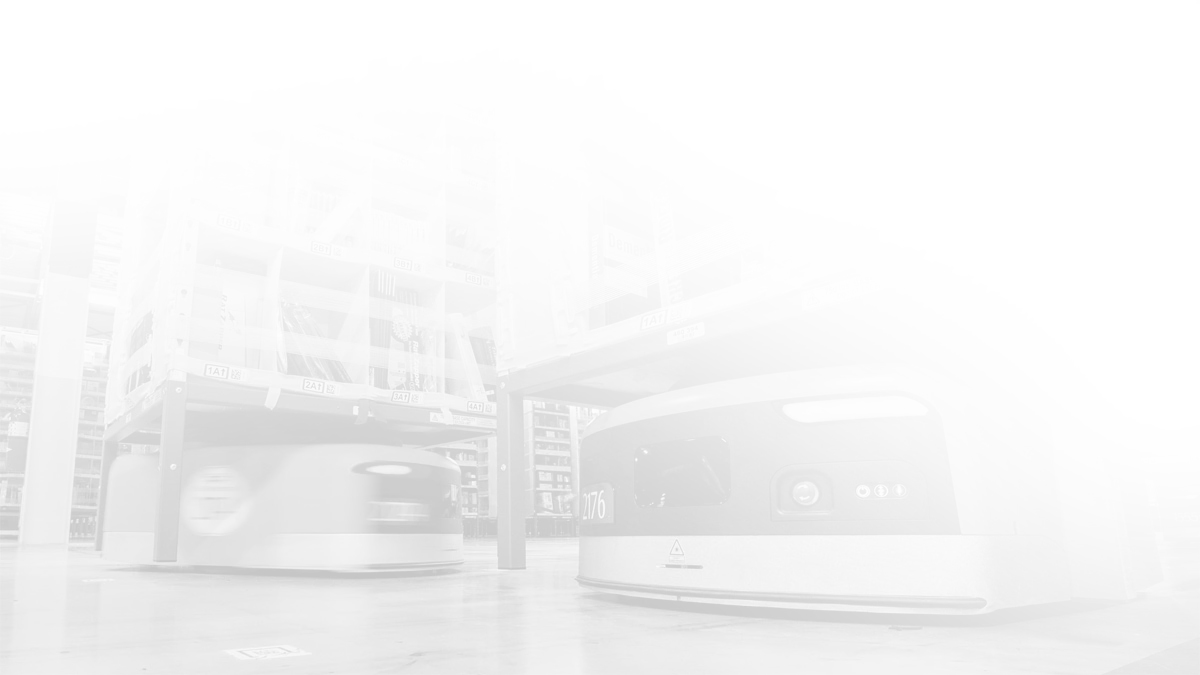
I sistemi di trasporto EOM (Eletric Overhead Monorail) chiamato anche di EMS (Eletric Monorail System), consistono principalmente in un sistema di rotaie aeree di alluminio sulle quali si muovono macchine motorizzate individuali. Ogni macchina possiede la sua scatola di controllo, cioè, sono indipendenti tra loro riguardo il movimento, essendo che l’alimentazione e il controllo delle macchine realizzato attraverso sbarramenti di induzione o per contatto, fissati su un sistema di rotaie Il comando e la gestione del traffico sono realizzati in modo centralizzato usando CLP.
Questo sistema è stato sviluppato principalmente per situazioni dove è necessario un trasporto rapido e intelligente, per lunghe distanze (includendo il trasporto tra varie aree o palazzi), senza ostruire vie e corridoi di accesso.
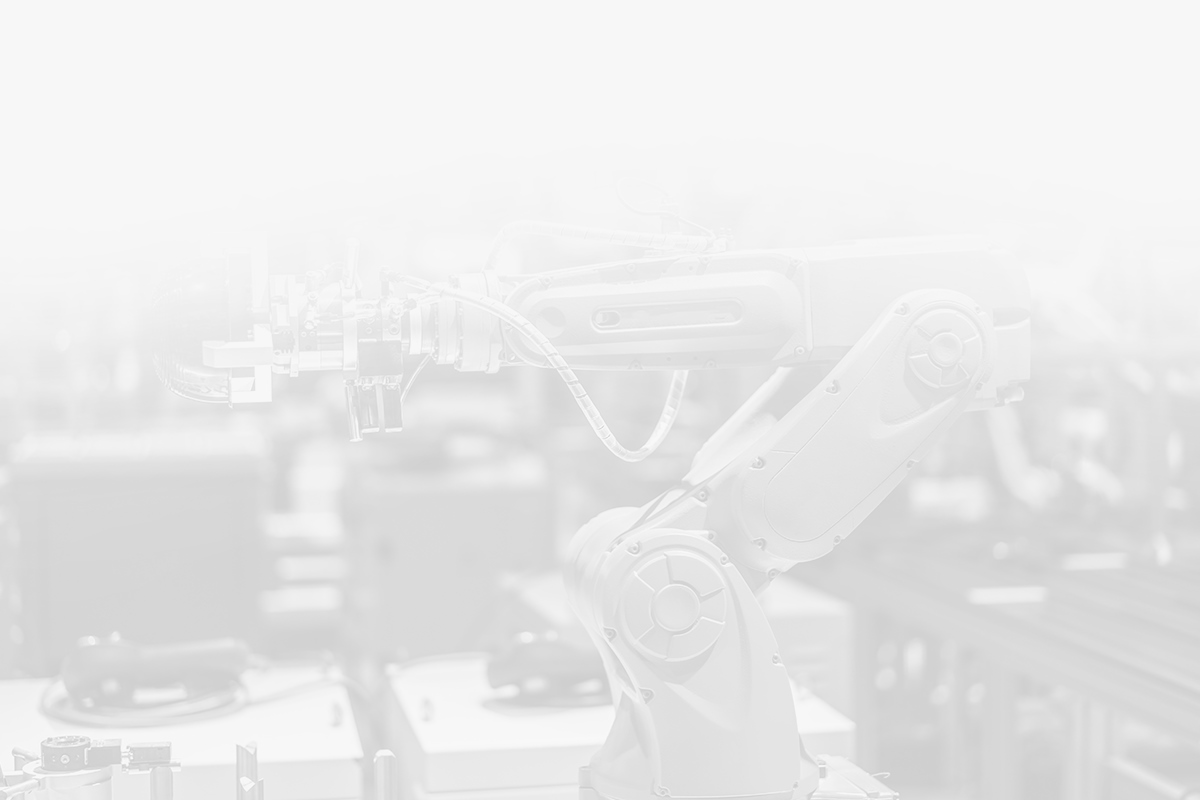
Al sistema basico di trasporto possono essere aggiunti dei disvii nella linea, elevatori, macchine di spostamento, svincoli giratori, ecc., garantendo una estrema versatilità al sistema, permettendo la comunicazione di tragitto e la direzione dei carichi o che garantisca che ogni carico sia presente nel processo esattamente nel tempo e nella cadenza necessaria.
Dentro ai principali settori e applicazioni possiamo distaccare l’industria automobilistica, per esempio la movimentazione e lo stock di carrozzerie, e alimentazione e stock di pezzi e componenti (carrozzeria, porte, ruote, ecc.) in linee di saldatura e in linee di montaggio finale.
Principali vantaggi
- Trasporto silenzioso e esente di vibrazioni
- Alta velocità di trasporto
- Monitoramento e selezionamento dei carichi
- Trasporto senza contaminazione dell’ambiente (olio, grasso, polvere, ecc.)
- Alta efficienza del sistema (in caso ci siano perdite di qualche macchina possono essere spostate nelle aree di manutenzione, lasciando libero il flusso dei materiali)
- Sicurezza, perché il sistema non interferisce con il traffico di persone e carichi al livello del pavimento
- Sistema di controllo intelligente, che permette rapide alterazioni nelle condizioni di flusso dei materiali
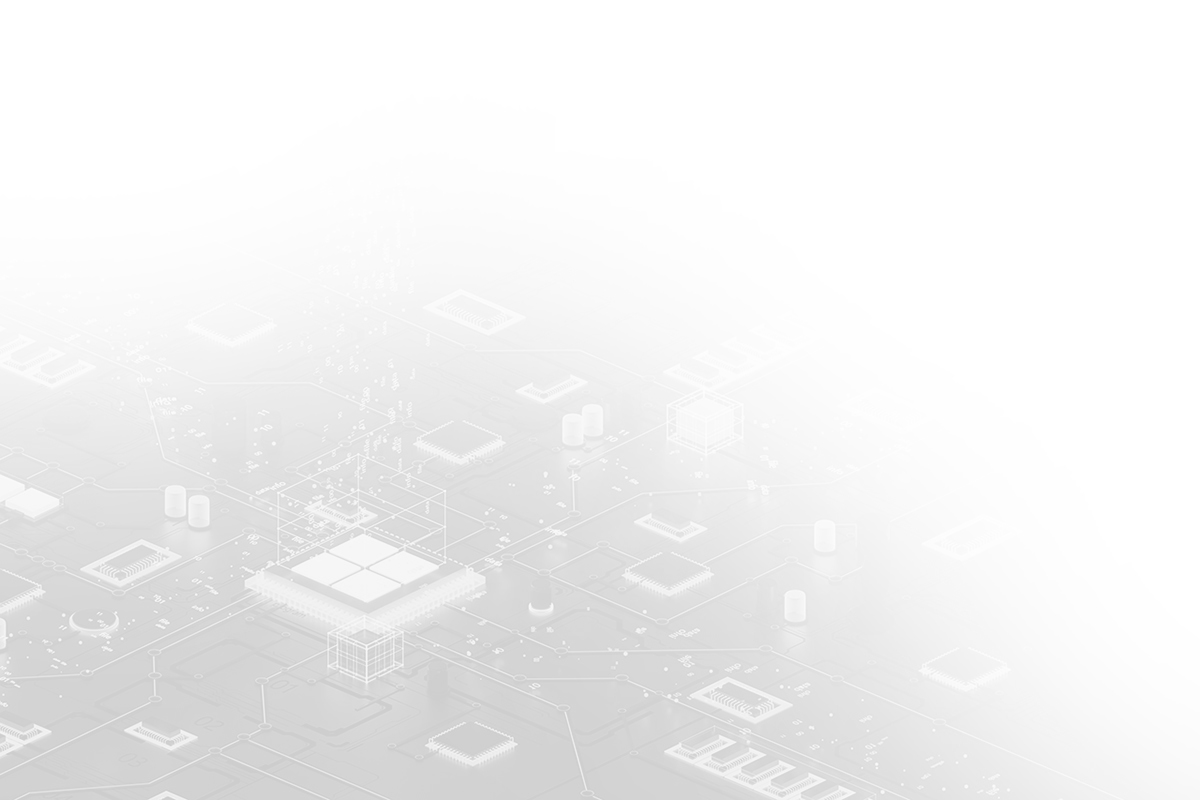
Power & Free
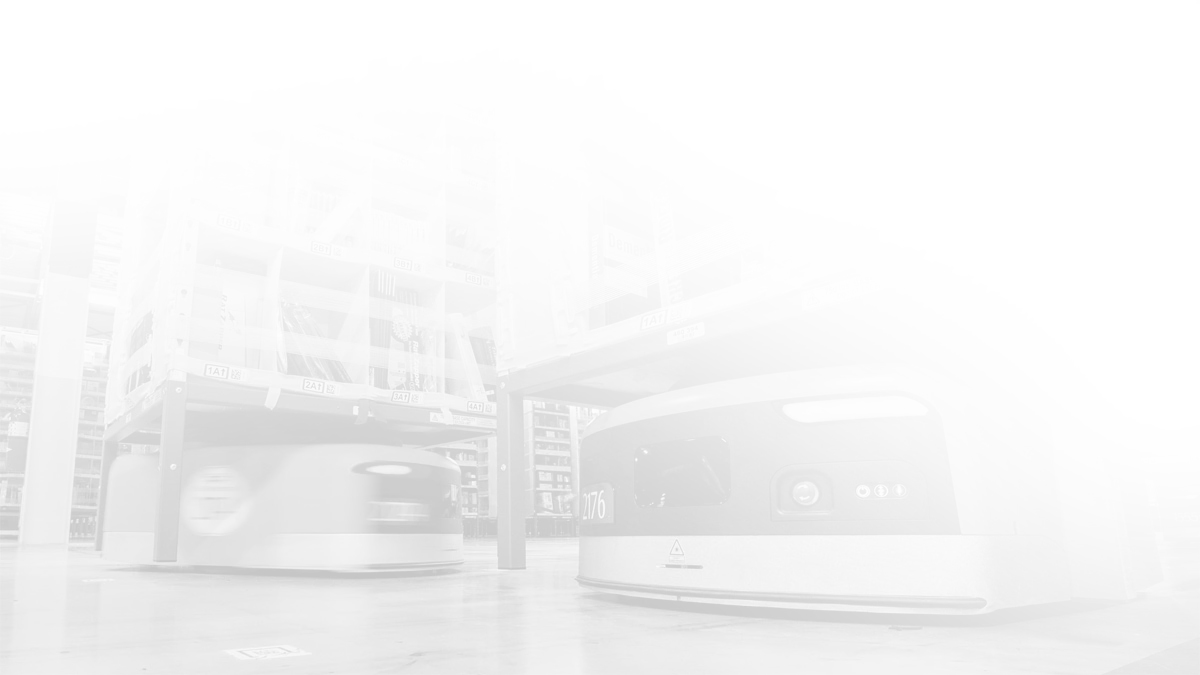
Il sistema Power & Free serve per movimentare pezzi e prodotti in aree di produzione, sia nelle stazioni sia nelle operazioni manuali. Basicamente il sistema Power & Free ha due rotaie una sopra l’altra. Sulla prima rotaia conosciuta come rotaia Power una catena trasportatrice circola ininterrottamente mentre il macchinario e’in funzione.
Nella seconda rotaia, i carichi che sono trasportati sono fissati a carrelli che si muovono su rotaia. Barre di carico uniscono due o piu’ carrelli per creare un unico carico. Per mezzo di un sistema di attacchi la catena superiore riesce a spingere i carrelli in accordo con le necessità. Nella eventuale presenza di carrelli davanti il sistema di attacchi si sgancia permettendo cosi l’accumulo dei carrelli sulla linea. Nei carrelli uniti uno all’altro i carichi sono trasportati su supporti, ceste o separatori. I carrelli possono essere aperti per caricare i prodotti. A seconda del carico trasportato, il sistema viene configurato con rotaie di 3, 4, e 6 pollici e sistemi di corde, potendo trasportare carichi fino a 9000 kg approssimatamente.
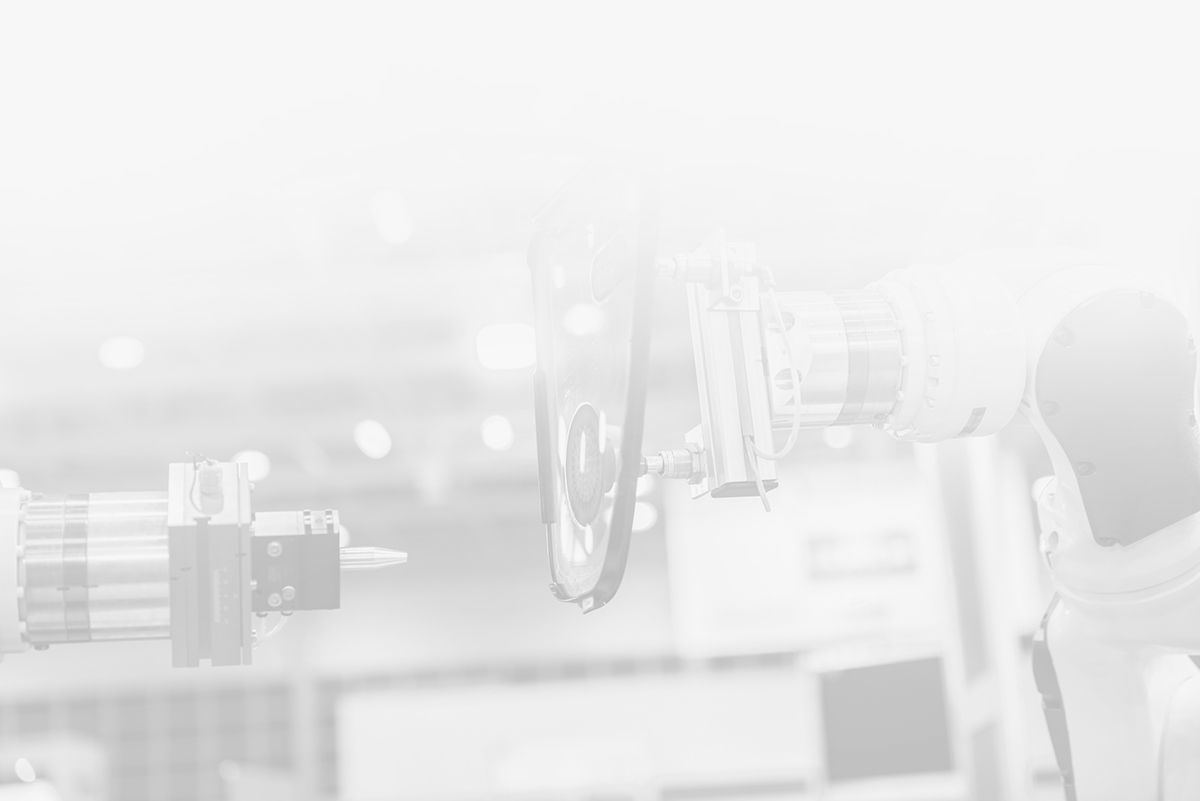
Il sistema di trasporto Power & free permette che i pezzi siano fermi o si muovano a velocità variabili in accordo con le necessita, in questo modo possono essere applicati concetti di produzione “stop and go” e anche di “Assembramenti a Velocita’Continua”. Le tipologie sono “Overhead” o invertite (montata sul terreno).
Il sistema Power & Free può essere utilizzato in vari processi produttivi, montaggio di attrezzature, pittura, saldatura, ecc.
Principali caratteristiche
- Sistema robusto per carichi pesanti
- Manutenzione semplice
- Opera in ambiente con umidità e alte temperature
- Alta disponibilità tecnica
- Tecnologia semplice con basso indice di automazione
- Curva verticale e orizzontale in accordo con le esigenze di profilo e processo
- Velocità variabili di trasporto per mezzo di variazione di velocità